The Impact of Advanced Tooling on CNC Productivity
Introduction CNC machining is at the heart of modern manufacturing, and advanced tooling is playing a critical role in boosting productivity, precision, and efficiency. As industries move towards high-performance machining, adopting next-generation cutting tools is no longer an option but a necessity.
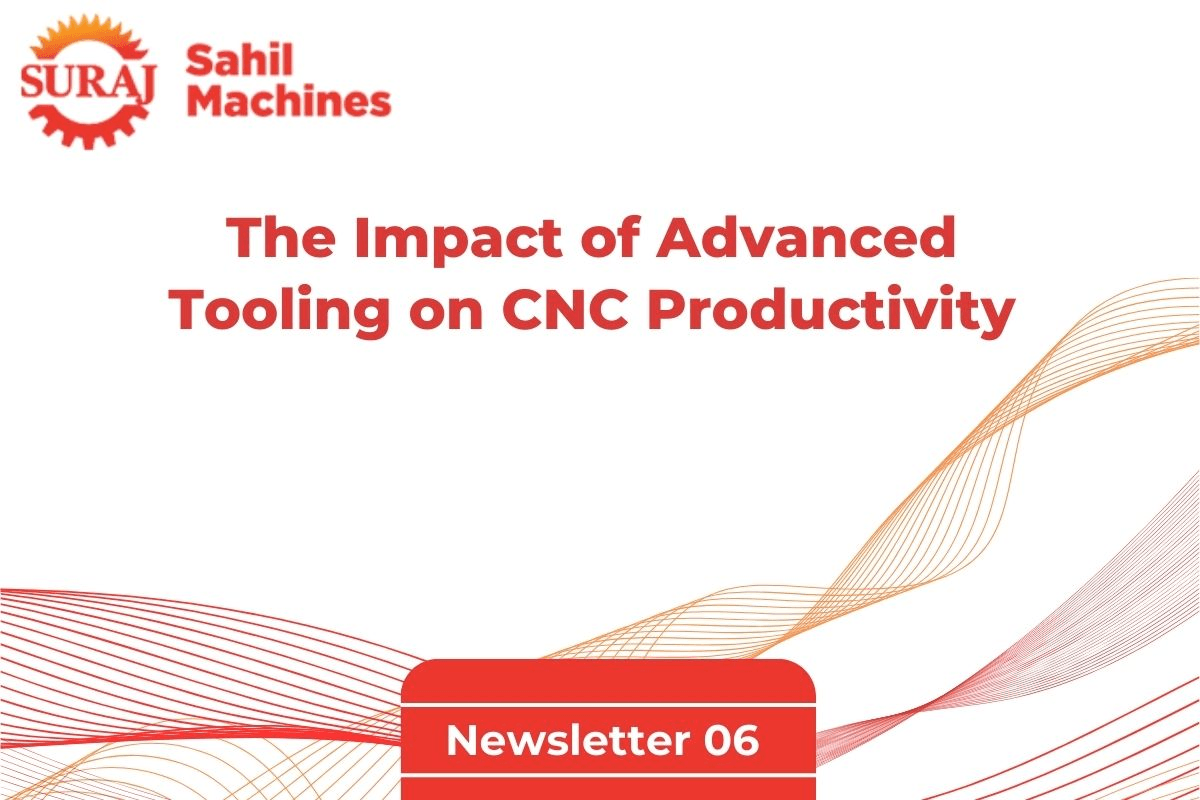
- High-Performance Cutting Tools for Faster Machining The demand for faster machining cycles and higher accuracy has led to the development of advanced cutting tools made from ultra-hard materials such as carbide, ceramic, and cubic boron nitride (CBN). Why Advanced Tooling Matters?
- Increased Cutting Speeds – High-speed tools reduce cycle times significantly.
- Extended Tool Life – Advanced coatings like TiAlN and DLC minimize wear.
- Enhanced Surface Finish – Less secondary processing required.
- Tool Coatings & Wear Resistance Modern CNC tooling is equipped with next-gen coatings that improve resistance against extreme temperatures and cutting forces.
- Diamond-Like Carbon (DLC) Coatings → Ideal for non-ferrous metals & composites.
- Aluminum Titanium Nitride (AlTiN) Coatings → Extends tool life in high-heat machining.
- Ceramic Coatings → Essential for aerospace-grade materials like titanium & Inconel.
- Toolpath Optimization with AI & Simulation CNC software is evolving to support AI-powered toolpath optimization, leading to higher efficiency and reduced waste.
- Benefits of AI-Optimized Tooling: Reduced Machining Time → AI algorithms optimize tool engagement.
- Lower Tool Wear → Intelligent feed rate adjustments prevent excessive wear.
- Improved Accuracy → Real-time adaptive adjustments ensure precision.
- The Rise of Smart Tooling & IoT Integration IoT-enabled smart tooling is transforming CNC machining by providing real-time data analytics for improved decision-making.
- Connected Tooling Systems → Sensors track wear & predict failures.
- Automated Tool Change Systems → Minimizes downtime & maximizes productivity.
- Cloud-Based Tool Monitoring → Enables remote diagnostics & maintenance.
- Sustainability & Tooling Innovations Sustainable CNC machining is gaining momentum, and advanced tooling is contributing to eco-friendly manufacturing practices.
- Sustainability Trends in CNC Tooling:
- Minimal Coolant Usage → Advanced coatings reduce reliance on lubricants.
- Recyclable Cutting Inserts → Reduces waste & manufacturing costs.
- Longer Tool Lifespan → Lowers material consumption & enhances efficiency.
Conclusion Advanced CNC tooling is revolutionizing machining by offering higher speeds, greater accuracy, and cost-efficiency. Manufacturers adopting next-gen cutting tools, AI-driven optimization, and smart tooling will gain a competitive edge in 2025 and beyond.
- Sahil Machines is at the forefront of CNC innovation, delivering high-precision solutions for industries worldwide.
- Visit us: www.sahilcnc.com
- Inquiries: info@sahilcnc.com
- Follow Sahil Machines for the latest CNC industry trends!
Published at: March 18, 2025
Latest News
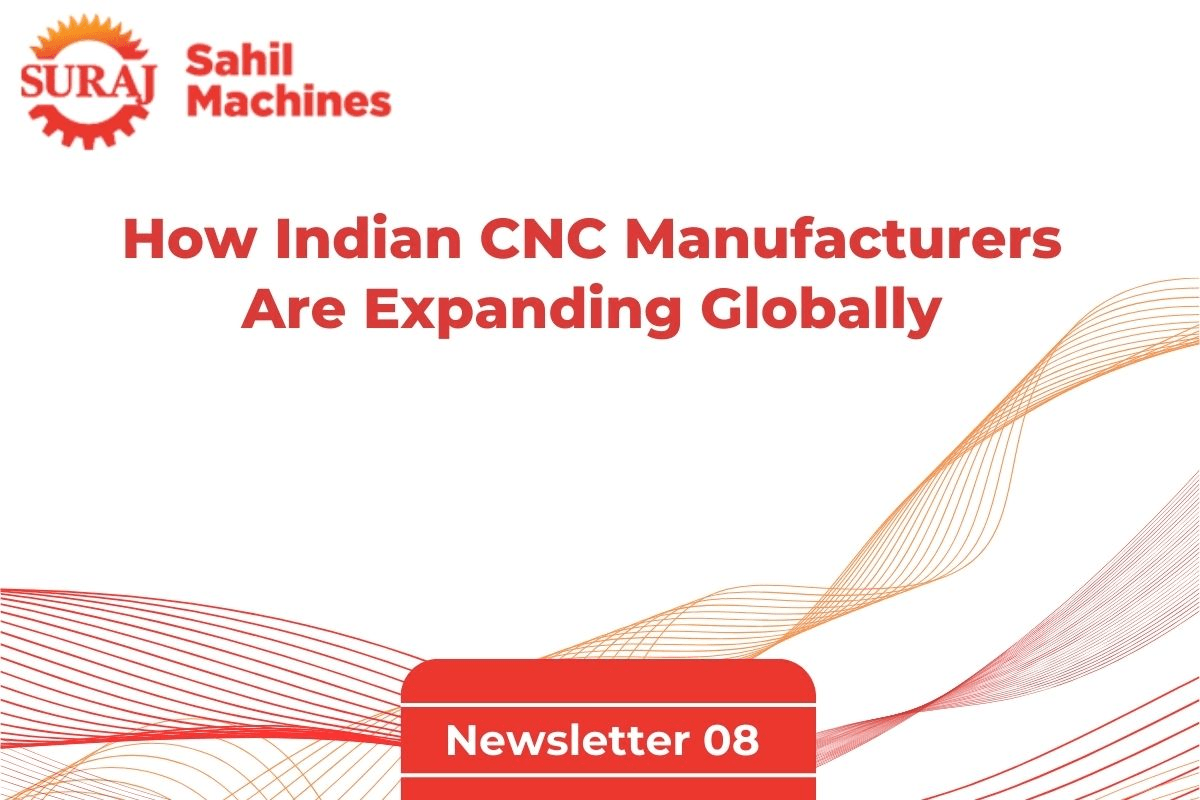
The Role of CNC Machining in Shipbuilding & Marine Engineering
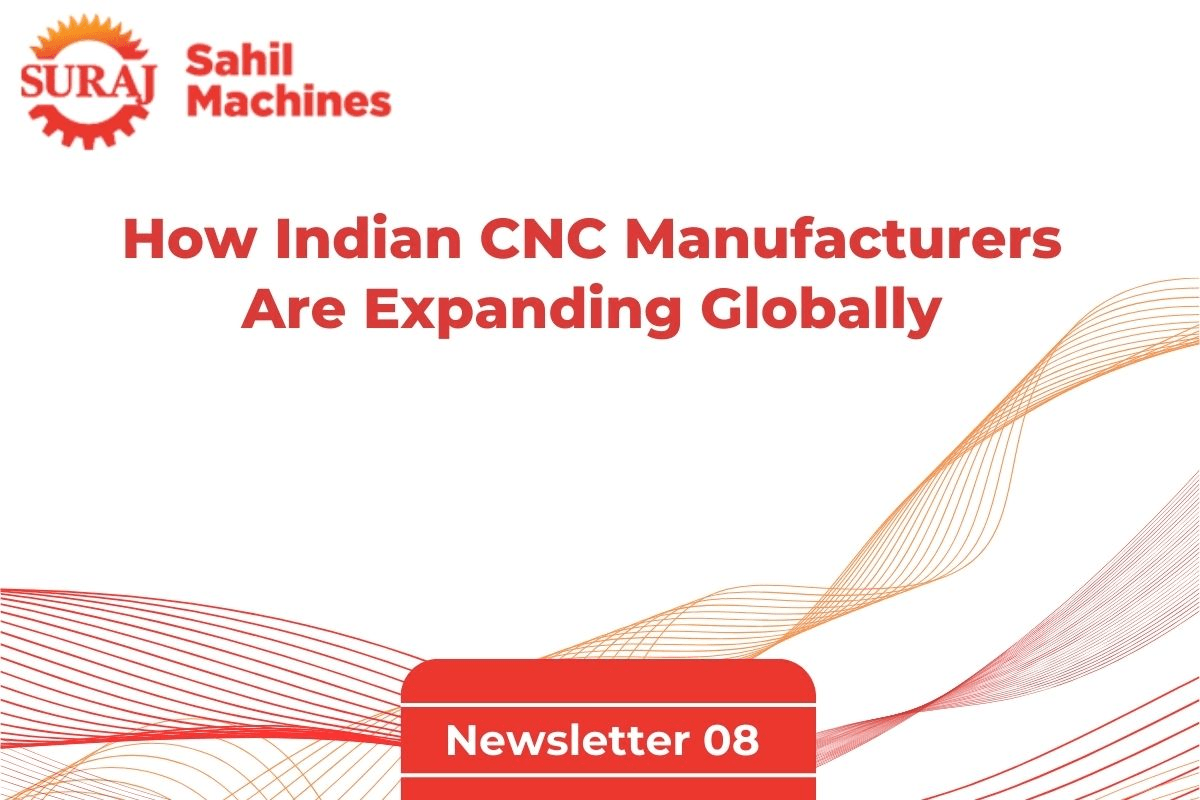
How Indian CNC Manufacturers Are Expanding Globally
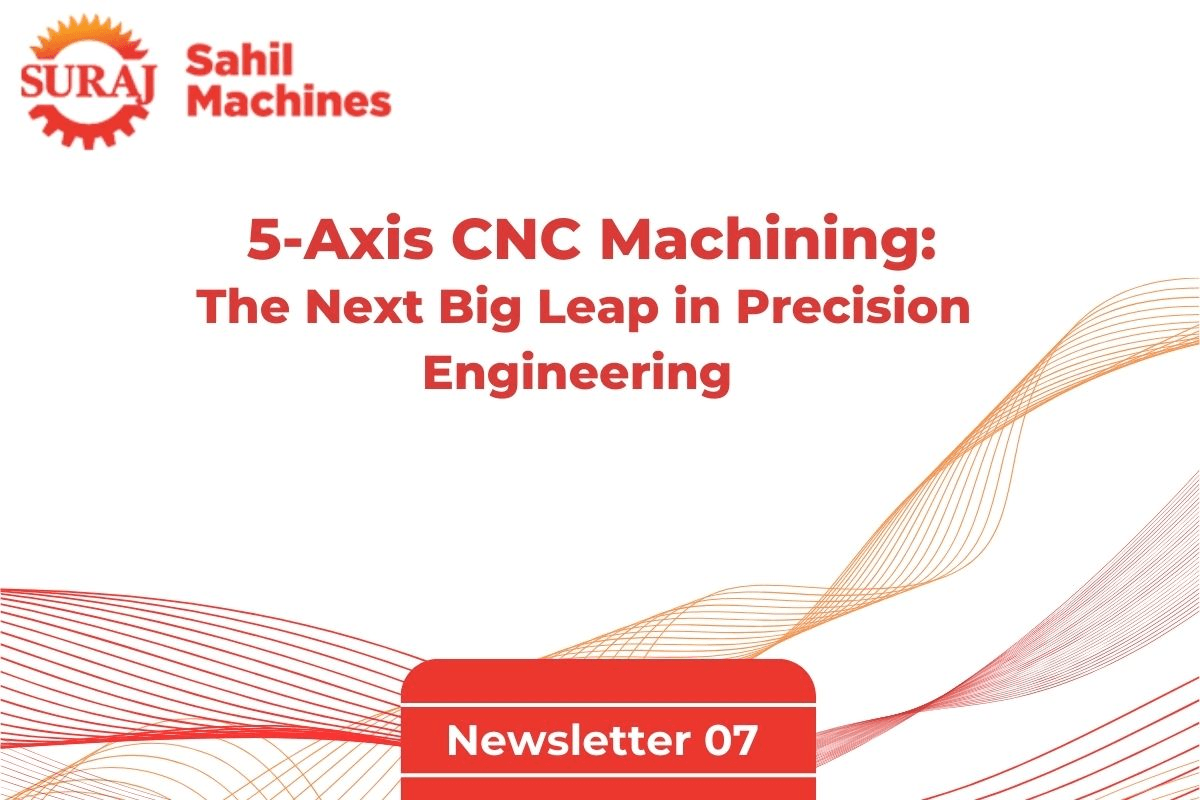
5-Axis CNC Machining: The Next Big Leap in Precision Engineering
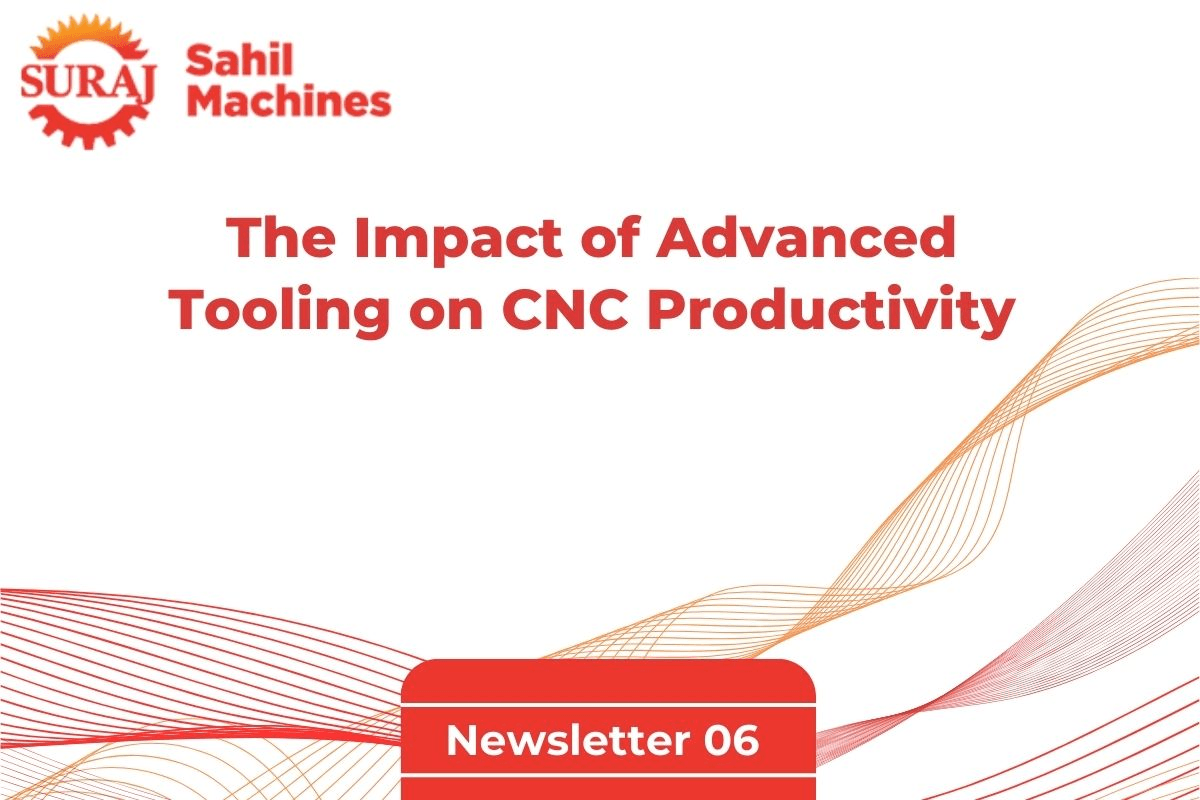
The Impact of Advanced Tooling on CNC Productivity
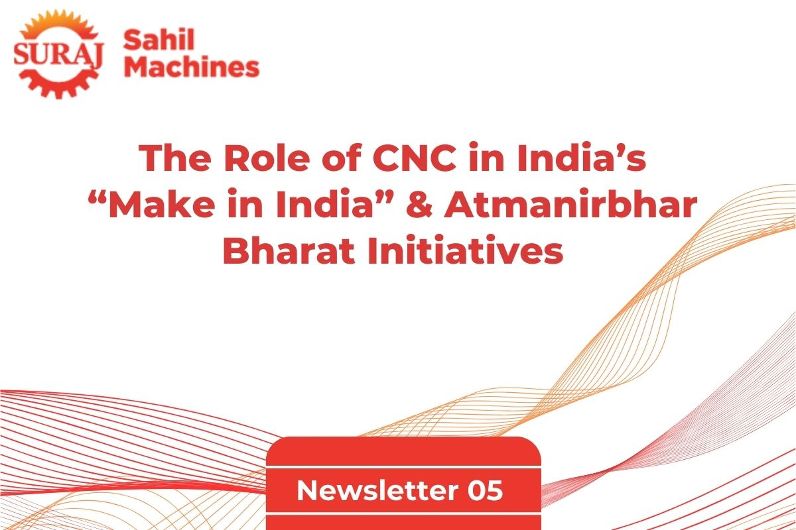
The Role of CNC in India’s “Make in India” & Atmanirbhar Bharat Initiatives
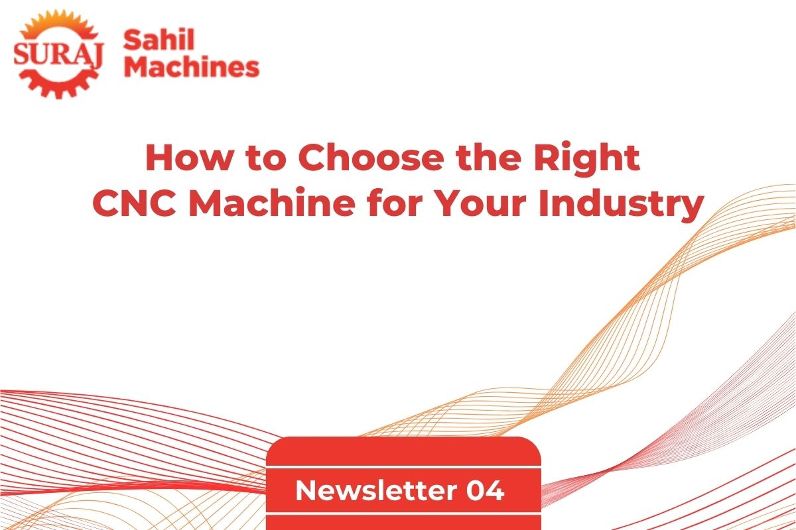
How to Choose the Right CNC Machine for Your Industry
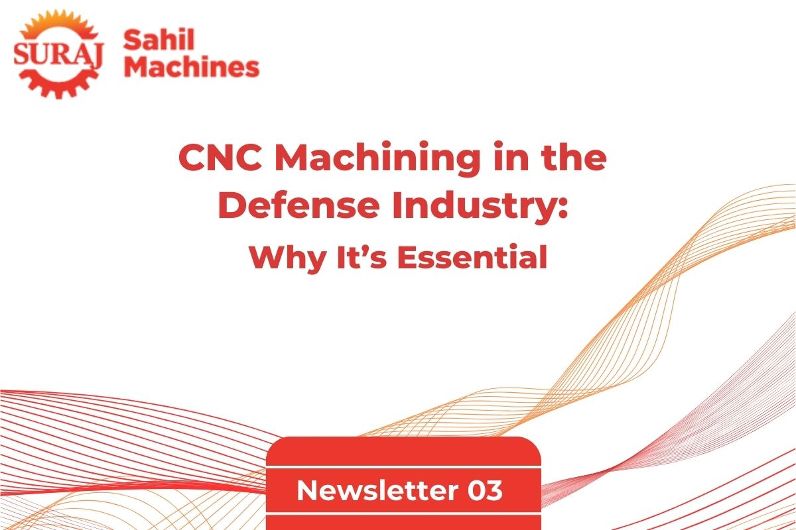
CNC Machining in the Defense Industry: Why It’s Essential
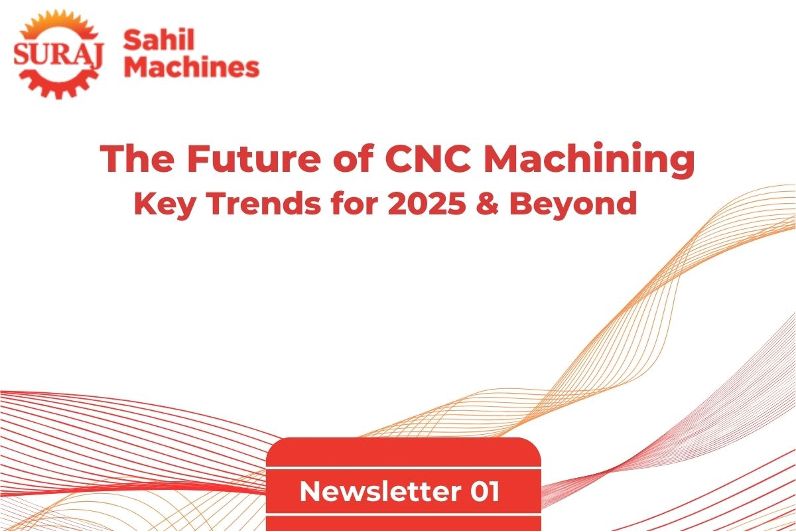
Growth of 5-Axis & Multi-Axis CNC Machines
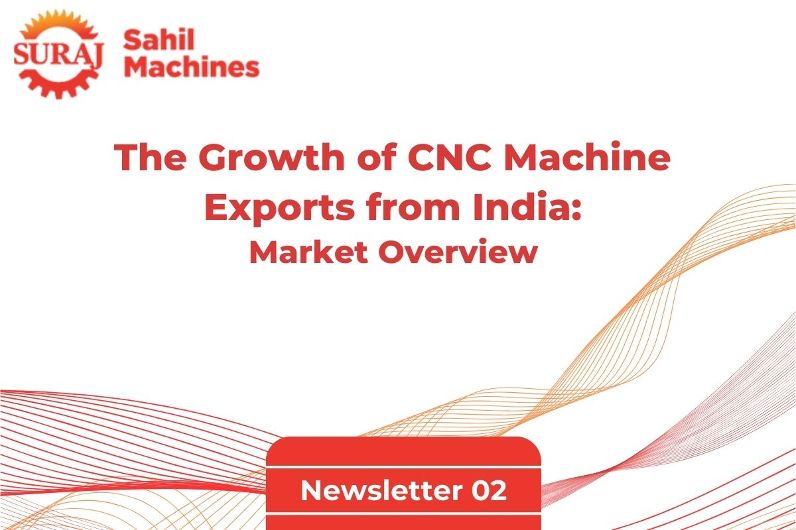
The Growth of CNC Machine Exports from India Market Overview
Get in touch with us about anything.
Connect with our team to explore the alloy solutions and machinery expertise you need.