CNC Machines: Transforming the Landscape of Modern Manufacturing
The contemporary manufacturing sector requires precision with automation for increased speed in the production process. A combination of precision and automation is exactly what a CNC machine offers.
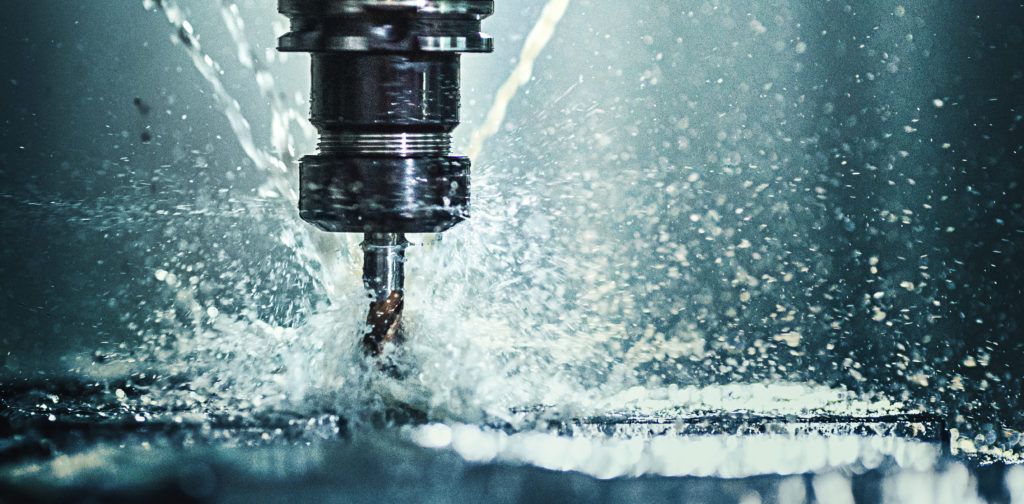
April 01, 2025
Share:
The contemporary manufacturing sector requires precision with automation for increased speed in the production process. A combination of precision and automation is exactly what a CNC machine offers.
What is CNC Machining?
A CNC (Computer Numerical Control) machine is a computer-controlled device that automates manufacturing. It follows a set of computerized instructions, which directs the machine to cut, shape, drill, or mill materials like metal, wood, or plastic. From the aerospace industry to the automotive industry, all of them are utilizing a CNC machine to stay at the top of the market.
Principles of a CNC Machine
The principle of a CNC (Computer Numerical Control) machine revolves around automating the machining process through computer programming. Here’s a simplified explanation of how it works:
Design and Programming
The process begins with creating a digital design of the part using CAD (Computer-Aided Design) software. It is then converted into G-code or M-code using CAM (Computer-Aided Manufacturing) software. These codes serve as detailed instructions for the CNC machine, specifying the exact movements and operations needed to produce the part.
Machine Setup
Material loading involves securely placing the workpiece material on the CNC machine's work table. Following this, the tool setup phase requires installing and calibrating the appropriate cutting tools or attachments based on the specific job requirements.
Automated Machining
The CNC machine executes the programmed instructions by automating the machining process and controlling the movement of tools and the workpiece along multiple axes (X, Y, Z, and sometimes additional axes). It performs precise movements according to the design specifications.
Monitoring and Adjustment
A proactive approach of real-time monitoring allows for immediate adjustments, maintaining the integrity of the production. The dual focus on real-time monitoring and post-machining inspection ensures high-quality and precise outcomes in CNC manufacturing.
Efficiency and Repeatability
CNC machines excel in consistent production by repeatedly producing identical parts with high precision, making them ideal for both small-scale and mass production.
Different Types of CNC Machines
CNC machines come in various types for different manufacturing processes and materials. Here are some of the most common types:
CNC Milling Machines
A CNC milling machine uses rotary cutters to remove material from a workpiece, performing operations like drilling, boring, and slotting. It operates on three to five axes (X, Y, Z, and sometimes A and B) and allows for precise and complex functioning.
CNC Lathes
A CNC lathe functions by rotating the workpiece while a cutting tool is applied to shape it, making it ideal for creating cylindrical parts. Typically, it operates on two axes (X and Z), although more advanced models may include additional axes for increased versatility and precision.
CNC Grinders
A grinding machine uses a rotating wheel to grind down materials. A high level of surface finish and accuracy can be achieved using CNC grinders. The axes of the machine can vary, with some models operating on multiple axes.
CNC Turning Center
Turning centers are notable for performing various lathe-cutting operations simultaneously on a rotating component. It enhances efficiency and productivity in the machining process.
CNC Boring
The CNC boring process involves expanding existing holes or internal cylindrical surfaces, typically using lathes or specialized equipment such as horizontal boring machines.
CNC Drilling
CNC drilling machines are perfect for mass production, as they can create or enlarge holes in various materials. There are two main types: the bench drill for drilling holes in small workpieces and the pillar drill, a larger model designed for drilling holes in larger workpieces.
CNC Routers
CNC routers are primarily used for cutting and shaping wood, plastics, and softer materials. Typically, CNC routers operate on three axes (X, Y, and Z), allowing for precise and intricate designs to be executed with high accuracy.
CNC EDM (Electrical Discharge Machining) Machines
A CNC Electrical Discharge Machining (EDM) uses electrical discharges (sparks) to erode material from a workpiece. Typically, EDM machines operate on two or three axes to achieve precise and complex cuts in hard materials.
CNC Plasma Cutters
A CNC plasma cutter uses a high-temperature plasma arc to cut through metal sheets. It operates on two or more axes, depending on the complexity of the cut, allowing for precise and versatile metal fabrication.
CNC 3D Printers
A CNC 3D printer builds parts layer by layer from additive materials like plastic or resin, based on a digital model. Typically, the machine operates on three axes: X, Y, and Z, allowing for precise and intricate creations.
CNC Laser Cutters
The function of this device is to use a laser beam to cut or engrave materials. It typically operates on two or three axes, making it ideal for precise cuts and detailed engravings on various surfaces.
Components of a CNC Machine
A CNC (Computer Numerical Control) machine is composed of several key components that work together to perform precise machining tasks. Here are the primary components and their functions:
- The Input Devices include the keyboard, mouse, and touch screen that allow operators to input commands and interact with the CNC system.
- The Machine Control Unit (MCU) is the brain of the CNC machine. It interprets instructions from the CAD/CAM software and converts them into electrical signals that control the machine's movements and operations.
- The Machine Tool is the part of the CNC machine that performs the cutting, drilling, milling, or other machining operations. It includes various types of tools, such as drills, lathes, and mills, which can be changed automatically or manually.
- The Drive System consists of motors and mechanical components like lead screws and ball screws that move the worktable and spindle. It ensures precise positioning and movement as per the MCU's instructions.
- The Coolant System supplies coolant to the cutting tool and workpiece to reduce heat and friction, which helps in prolonging tool life and ensuring a better surface finish.
- The Feedback System includes sensors and encoders that provide real-time feedback to the MCU about the machine's position and operation. It helps in maintaining accuracy and correcting any deviations.
- The Control Panel allows the operator to control the CNC machine, start and stop operations, and monitor the machining process. It often includes an emergency stop button for safety.
Check out a wide range of CNC machines at Sahil Machines.
Whether you’re a small business or a large enterprise, CNC machines are going to streamline your manufacturing experience. Here is a quick look at why you should upscale your manufacturing sector with CNC machines.
Benefits of CNC Machines
CNC machines offer several advantages over traditional manual machining methods. Here are some key benefits:
Precision and Productivity
CNC machines excel in producing parts with very tight tolerances and high accuracy, making them essential for complex and intricate designs. They also ensure uniform production by consistently reproducing the same part with consistent quality.
Automation and Speed
This combination of precision and automation ensures reliable and high-quality output. CNC machines significantly cut production time by operating at high speeds and performing multiple operations simultaneously. They make the manufacturing process easy and improve productivity.
Cost-Effectiveness and Reduced Labour
The combination of automation and speed further optimizes resource utilization. It leads to cost savings and increased output, cutting production time significantly.
Customization and Efficiency
With advanced programming capabilities, CNC machines can be easily reconfigured to create a wide variety of designs, allowing for rapid adjustments and prototyping. The automation of CNC machines significantly enhances efficiency by minimizing human intervention, reducing errors, and optimizing material usage.
Reduced Waste and Flexibility
Material efficiency is a significant advantage of CNC machines, as their precise control minimizes material wastage by cutting exactly according to the design specifications. Additionally, straightforward and efficient reprogramming can be done quickly in CNC Machines. This flexibility not only saves time but also enhances overall productivity.
These advantages make CNC machines a valuable asset in various industries, including aerospace, automotive, and manufacturing, where precision and efficiency are critical.
Disadvantages of CNC Machines
While CNC machines offer numerous benefits, they also come with some disadvantages:
Maintenance and Cost
The initial investment in a CNC machine can be quite high. It might be quite challenging to invest as a startup or small business. Further, maintaining a CNC machine can be challenging.
Complexity and Constraints
A CNC machine requires skilled operators to program and run the machine. It is limited to tasks that can be pre-programmed. Further, a software or hardware glitch can disrupt production and might be time-consuming.
Limited Workpiece Size
Certain CNC machines cannot accommodate large workpieces and so it is crucial to do your research and select the right machine for your requirements.
Increased Power Consumption
CNC machines require a stable and substantial power supply to operate, which can lead to high energy consumption. Efficient power management and the use of energy-efficient models can help mitigate these costs.
Despite these disadvantages, the overall efficiency, precision, and automation benefits of CNC machines often outweigh the drawbacks, especially in high-volume and complex manufacturing environments.
How Does it Work?
Here’s a simplified breakdown of how a CNC machine works, presented in pointers:
- Create a detailed digital design of the part or product using Computer-Aided Design (CAD) software.
- Convert the CAD design into machine-readable code (G-code or M-code) using Computer-Aided Manufacturing (CAM) software.
- Place the workpiece material onto the CNC machine's bed or fixture securely. Further, necessary cutting tools or attachments are installed and calibrated to ensure precise machining.
- Load the generated code into the CNC machine’s control system. The machine then moves tools or the workpiece according to these programmed instructions to achieve the specific design.
- Monitor the operation to ensure it adheres to the specifications and to identify any potential issues.
- The post-processing involves applying finishing touches such as sanding, coating, or additional inspection to achieve the final desired quality and appearance of the part.
- The finished part is ready for further use or assembly once removed from the machine.
CNC Machines are a great asset to the manufacturing industry, offering precision, automation, efficiency, and increased productivity. The requirement for CNC machines in India is rapidly growing due to the country's expanding manufacturing sector. This technology is essential for industries like automotive, aerospace, and electronics, driving innovation and competitiveness in the global market.
Why choose Sahil Machines?
Choosing and selecting the right CNC (Computer Numerical Control) machine as per your needs is all that you want. Well, we want the same, for you to have a precise and fast manufacturing experience.
At Sahil Machines, we ensure you receive top-quality products. Backed by years of industry experience, we offer advanced CNC machines that deliver exceptional precision, reliability, and efficiency, tailored to meet the unique demands of your operations. Sahil Machines offers customizable solutions that meet the diverse requirements of customers across industries.
CNC machines signify a groundbreaking advancement in modern manufacturing, providing unmatched precision, efficiency, and versatility. They are key to achieving superior manufacturing standards. As technology continues to evolve, CNC machines will likely become even more advanced, further driving innovation and efficiency in the manufacturing sector.
FAQ
CNC machines can work with a variety of materials including metals, plastics, wood, composites, and ceramics.
Yes, CNC machines are versatile and can be used for both small-scale and large-scale production, making them suitable for various business sizes and production needs.
Investing in CNC machines can significantly enhance your manufacturing capabilities by improving precision, efficiency, and productivity. They reduce labor costs and material waste while enabling the production of complex parts.
Assess your specific production requirements, budget, space availability, and future growth plans. Consulting with us can help you make an informed decision.
Operators need skills in CNC programming (G-code/M-code), CAD/CAM software, machine setup, tool selection, and quality control. Training is often required.
Follow Us:
Latest Posts
Get in touch with us about anything.
Connect with our team to explore the alloy solutions and machinery expertise you need.