Top 5 Innovations in CNC Turning Machines for Precision Engineering
The article highlights five key innovations transforming CNC turning: multi-axis capabilities, hybrid machines, live tooling, advanced automation, and high-speed spindles.
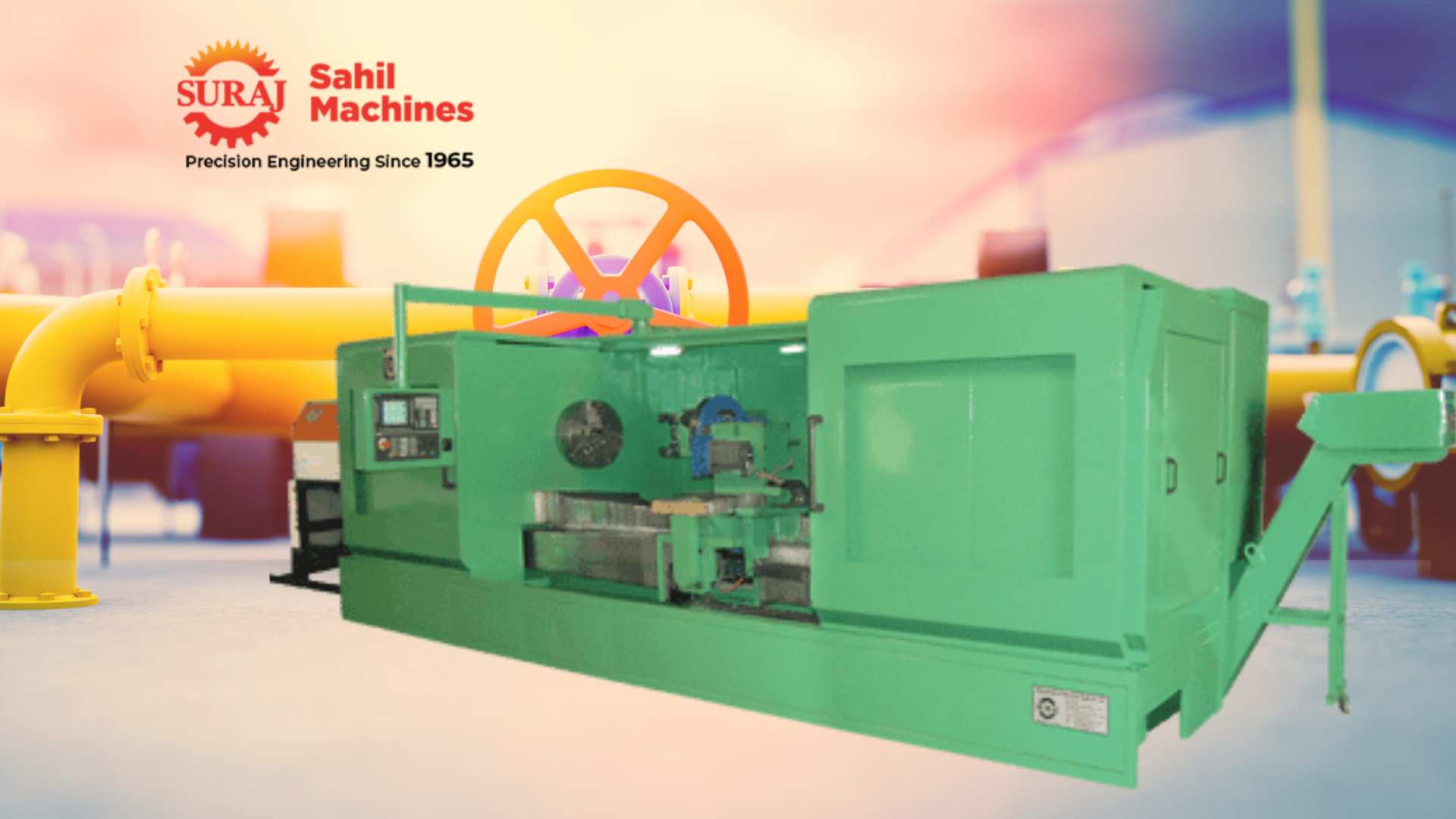
April 01, 2025
Share:
Although CNC turning machines have conventionally formed the backbone of manufacturing processes in precision engineering, they have continued to provide high accuracy, automation, and efficiency in making complex parts. However, the landscape of CNC turning keeps changing with new groundbreaking innovations that push the envelope of what is considered possible in precision machining. The following discussions highlight five innovative functionalities that reshape the outlook of the CNC turning industry and change manufacturing processes forever.
1. Multi-Axis CNC Turning
Another huge leap in the technology of CNC turning has to do with multi-axes capability. Most older generations of CNC lathes could always process on two axes, X and Z, which greatly limited the geometries that could be created on the Class Name. Nowadays, modern CNC turning machines can have as many as nine axes, including the Y and CA-axis for opening a completely new realm of possibilities when making intricate parts.
Key Benefits of Using Multi-axis CNC Turning
Improved Accuracy: Multi-axis machines can machine very complicated parts with such a level of precision that enables tighter tolerances and more complicated designs.
Reduced Setups: Parts, that required several machine setups before, can now be produced in a single operation with complex parts, reducing human intervention and, thus, increasing the accuracy of the work.
Improved Productivity: The ultimate benefit in this respect of multi-axis CNC turning machines is the reduction in setup times and an allowance for several operations in one go, doubling or tripling cycle times.
2. Hybrid CNC Turning Machines
Hybrid CNC machines are a shift in the paradigm of manufacturing. They take additive manufacturing regarded by some as 3-D printing, and put it together with traditional subtractive manufacturing methods, such as turning. This, in turn, has revolutionized the design and fabrication of complex parts because engineers can now build components in layers and then refine them with secondary precision turning processes.
Key Benefits of the Hybrid CNC Turning Machines
Versatility: Unparalleled is the versatility, which realizes high-precision finishes using both additive and subtractive rapid prototyping processes and complex geometries, correspondingly.
Cost-effectiveness: Hybrid machines save material waste by adding up the parts instead of cutting them out from solid blocks; this makes the manufacturing process cost-effective.
Greater design freedom: It consists of the ability to fabricate shapes and internal features that were impossible or impractical to manufacture by traditional methods only.
3. Improving Flexibility and Efficiency
Live tooling has revolutionized CNC turning by allowing machines to mill, drill, and tap without necessarily removing the workpiece. This novelty minimizes workflow interruptions and gives a whole new dimension to the turning operation.
Key Benefits of Live Tooling:
Increased Efficiency: Eliminating part transfers between machines reduces downtime and eliminates many secondary operations immediately benefiting from the use of live tooling.
Reduced Tool Wear: Optimized tooling for various operations in one setup results in better tool utilization and prolongs tool life. Streamlined Production: Many operations can be performed in one setup, reducing lead times and increasing the flexibility of production.
4. Powering Advanced Automation
With the integration of AI, machine learning, and IoT into the CNC turning machines, there was a huge advancement in precision and automation. Advanced state-of-the-art CAM software makes simulation even better, and does real-time monitoring, and predictive maintenance combined to make CNC turning very high on efficiency and accuracy.
Key Benefits of Advanced Software and Automation:
Precision Monitoring: Real-time data collection and analysis during the machining process ensure high accuracy at all times, with immediate adjustments possible at all junctures if required.
Fully Automated Optimization of Toolpaths: AI-driven software automatically optimizes the tool paths, reducing errors and resulting in complex surface finishes without human intervention.
Predictive Maintenance: The continuous monitoring of machine performance and wear indicators enables predictive maintenance to avoid expensive downtowns, prolonging machines' lives.
5. Pushing the Limits of Speed and Precision
Recent improvements in spindle technology now allow CNC turning machines to run much faster without sacrificing accuracy. High-speed spindles operate at much higher RPMs than standard spindles, offering higher material removal rates and better surface quality.
Key Benefits of High-Speed Spindle Technology:
Reduced Cycle Times: Faster cutting speeds translate into more productivity and shorter production cycles.
Improved surface quality: High-speed spindles can achieve better finishes on complicated geometries that eliminate the need for secondary finishing operations in many cases.
Better Material Flexibility: Tough materials, such as titanium, stainless steel, and hardened alloys, further extend the application of the CNC turning method in their performance.
The Future of CNC Turning
Linked with hybrid manufacturing, live tooling, advanced software integration, and high-speed spindle technology, these frontiers are changing the face of CNC turning. We expect more amazing developments to come over the next few years.
With these innovations, precision, efficiency, and flexibility are taken to higher levels in manufacturing processes. It follows that it would be not only better products produced but also competitiveness at the enterprise level to meet the ever-increasing demands of the industry today.
Why choose Sahil Machines?
Choosing and selecting the right CNC vertical turn-mill machines is your topmost priority. Well, we want the same, for you to have an efficient and fast manufacturing experience.
At Sahil Machines, we ensure you receive top-quality products. Backed by years of industry experience, we offer advanced Gantry Milling machines that deliver exceptional precision, reliability, and efficiency, designed to meet the unique demands of your operations. Sahil Machines offers customizable solutions that meet the diverse requirements of customers across industries.
Rest assured, in times to come, CNC turning will continue being at the head of the manufacturing field. By keeping up with such developments and integrating the same into the working processes, you can assuredly stand at the forefront of precision engineering.
Explore our advanced CNC turning solutions to revolutionize your manufacturing process. Contact Sahil Machines today for customized CNC solutions tailored to your needs!
Check out our FLAT BED series as well: https://www.sahilcnc.com/turning-machines/cnc-flat-bed-lathes/cfl-series/
FAQ
Yes, modern multi-axis CNC turning machines can produce intricate geometries, including grooves, tapers, and undercuts with high precision.
Automation reduces setup and machining times, enabling faster production cycles and 24/7 operation with minimal human intervention.
Consider part complexity, material type, production volume, spindle speed, number of axes, automation features, and budget.
They can handle metals like aluminum, steel, copper, brass, and titanium, as well as plastics, composites, and ceramics.
With proper maintenance, CNC turning machines can last 10–20 years or more.
Follow Us:
Latest Posts
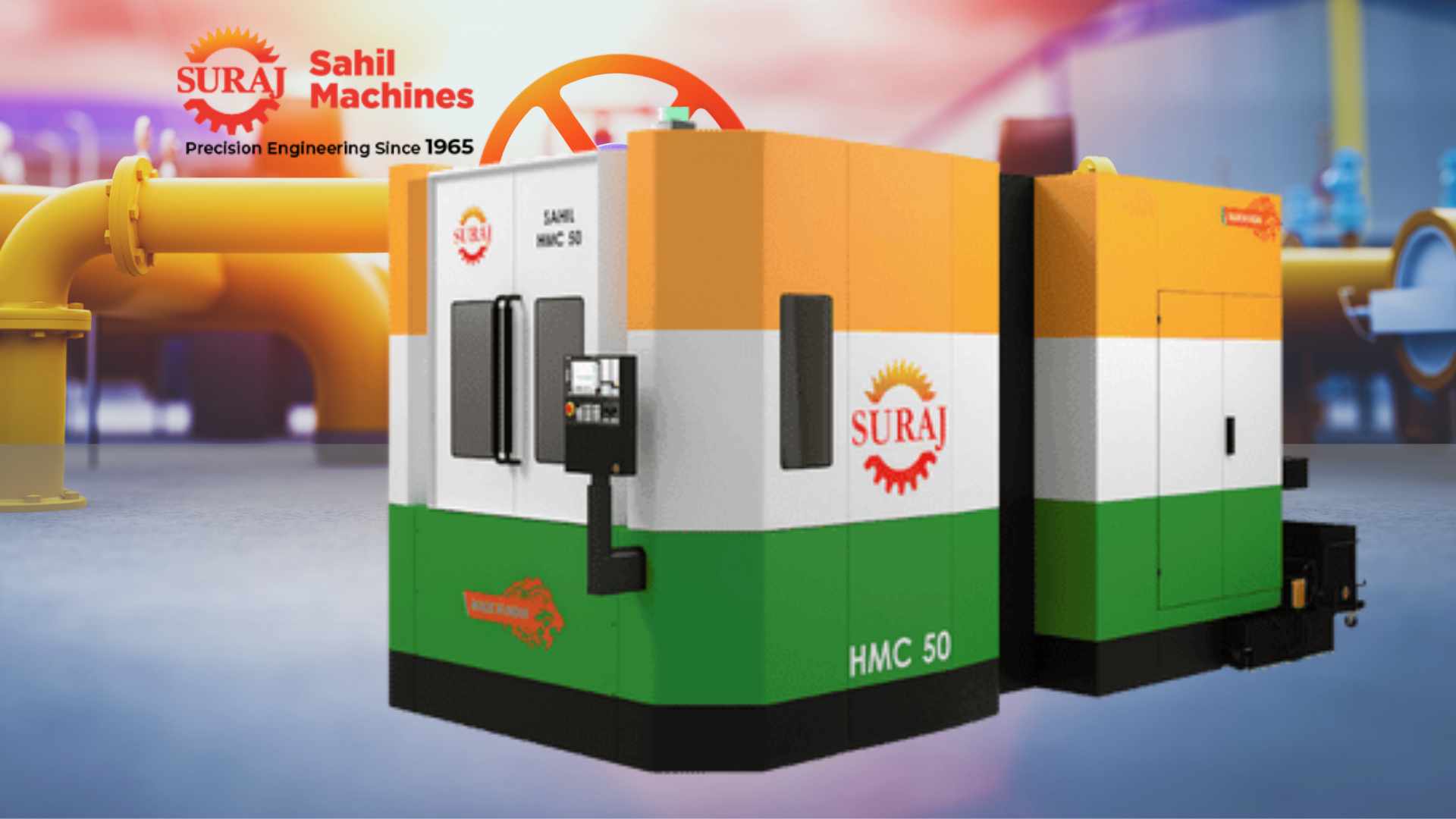
Get in touch with us about anything.
Connect with our team to explore the alloy solutions and machinery expertise you need.