Thread Milling vs Tapping: Which Threading Method is Right for You?
Precision manufacturing is crucial for the industrial sector. From aerospace to automotive, they all require high-quality threads to ensure the integrity, safety, and performance of critical components. Among the most common techniques are thread milling and tapping, but which will be best for your project?
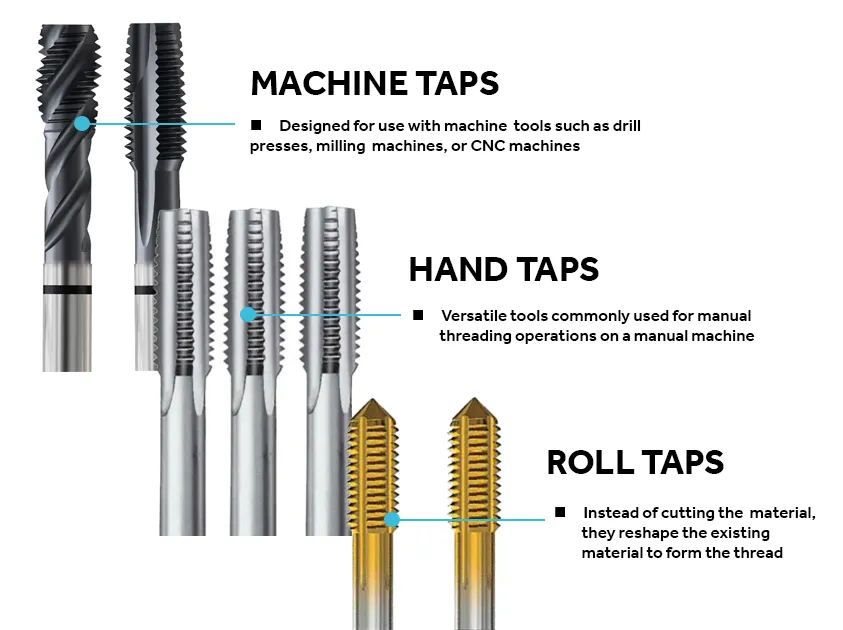
April 01, 2025
Share:
Precision manufacturing is crucial for the industrial sector. From aerospace to automotive, they all require high-quality threads to ensure the integrity, safety, and performance of critical components. Among the most common techniques are thread milling and tapping, but which will be best for your project? Threading can either be done by milling or tapping. Both techniques have pros and cons that one may want to consider.
What is Thread Milling?
Thread milling is one of the modem methods of machining. Here, threads are generated with a rotating multi-point cutting tool with its motion in a helical path. It plays an important role in the past decade due to its versatility and precision.
Advantages of Thread Milling
The advantages of thread milling include flexibility because one tool often can machine a wide range of thread sizes and pitches. It can be a great way to cut tooling costs and reduce setup times significantly.
Superior Thread Quality
Thread milling can result in threads with superior quality, superior surface finish, and full tolerance. Such industries that require superior precision include the aerospace and automotive ones.
Reduced Risk of Tool Breakage
Thread milling reduces the risk of tool breakage by distributing cutting forces more evenly, especially in harder materials.
Suitability for tough materials
Thread milling proves its utility in hard-tomachine materials, such as titanium and stainless steel, where one might not easily or confidently tap as they would with more cooperative materials.
Thread Repair Capabilities
Have a damaged thread that needs repair? Thread milling can often save the day with efficient thread repair, without scrapping an entire part. Limitations of Thread Milling
Higher Initial Costs
Thread milling usually requires CNC machinery; special tools may also be required, which implies higher initial costs.
Complexity
It requires more sophisticated programming and setup with an operator who has great experience in the overall technology dealing with CNC.
Slower for Small Threads
In the creation of small, fine-pitch threads, thread milling is more time-consuming than the traditional methods of tapping.
The Tapping Technique
Decades passed and the tapping technique has remained one of the favorites due to its simplicity and effectiveness. The tapping technique turns a cutting tool into an internally threaded hole using a screwlike cutting tool, or tap.
Advantages of Tapping
Speed Small thread size and soft material tapping are generally done faster, hence suitable for high-volume production.
Simplicity
Tapping is simpler in several ways to set up and operate as there is significantly less complex machinery and programming than there is in thread milling.
Cost-Effectiveness
Tapping tools are always cheaper as compared to thread milling cutters, hence more economically viable in many applications.
Soft material efficiency
Softer materials, such as aluminum or brass, can be tapped very effectively and quickly since threads come out neat and clean.
Limitations of Tapping
Material Limitations
Tapping into extremely hard materials is difficult; the risk of the tool breaking and efficiency is lowered.
Inflexibility
Every tap is designed to work for a certain thread size and type, requiring a couple of tools for different thread specifications.
Thread quality
The tapping usually creates threads that are of lesser quality or less accurate, particularly in stronger materials.
Chip Evacuation Problems
The deeper the holes, the more problematic the chip eviction becomes and results in poor quality of thread or even tool breakage. Choosing the Right Method for Your Project OK then, how do you know whether to thread mill or tap?
Material Properties
Is your workpiece made of some soft metal like aluminum or is it made from some tough alloy like titanium? Thread milling works well with hardened materials, and in turn, tapping works well on softer ones.
Specifications of Thread
Are you tasked with producing a wide array of thread sizes and pitches? In that regard, thread milling is far more flexible. Tapping will be required into action for tapping in high-volume continuous production of identical thread size. Thread milling is best in low to medium-volume production runs with varied specifications.
Machinery Available
Are there CNC machines available? Generally speaking, thread milling requires better machinery than that used for tapping.
Cost Factors
Compare the initial tooling costs of each method, both with respect to one another and in terms of the ongoing production costs.
Thread Depth
However, thread milling might offer improved chip evacuation with deeper threads, reducing breakage possibilities.
Surface Finish Requirements
If superior surface finish is to be attained, then thread milling will probably provide a better result.
Conclusion
While both thread milling and tapping find their place in contemporary manufacturing, the former technique offers unparalleled flexibility, precision, and performance on tough materials. Ideally, it is the perfect method for industries requiring high-quality, varied threads. Tapping supplies a faster, simpler method of creating internal threads in softer materials, especially in high-volume production environments.
The decision on whether thread milling or tapping comes down to the individual application, material type, volume of output, and investment in machinery. Careful consideration of these factors will enable you to choose correctly for the right approach that can best acquire excellent results for your threading needs and continue to enhance the efficiency, quality, and productivity of your operations.
Why choose Sahil Machines?
Choosing and selecting the right machines is your topmost priority. Well, we want the same, for you to have an efficient and fast manufacturing experience.
At Sahil Machines, we ensure you receive top-quality products. Backed by years of industry experience, we offer advanced CNC machines that deliver exceptional precision, reliability, and efficiency, designed to meet the unique demands of your operations. Sahil Machines offers customizable solutions that meet the diverse requirements of customers across industries.
Whether you are manufacturing critical parts for the aerospace industry, or producing high-volume components in automotive, knowledge of each threading method's strengths and limitations will help you make an informed decision. The next time you face a threading challenge, you will know precisely which tool to reach for, whether it's a state-of-the-art thread mill or a reliable tap.
Where precision manufacturing is involved, the right method to thread can sometimes mean just the difference between a good part and a great one.
FAQ
Thread milling is ideal for hard materials due to its reduced risk of tool breakage and superior thread quality.
Tapping is best for high-volume production, small threads, and softer materials like aluminum and brass, as it is faster and more cost-effective.
Yes, one thread mill can create multiple thread sizes and pitches, whereas tapping requires a different tool for each size.
Thread milling generally produces superior thread quality and better surface finishes, making it ideal for precision applications.
Tapping has lower initial tooling costs and is more economical for high-volume production, while thread milling offers long-term savings by reducing tool breakage and increasing versatility.
Follow Us:
Latest Posts
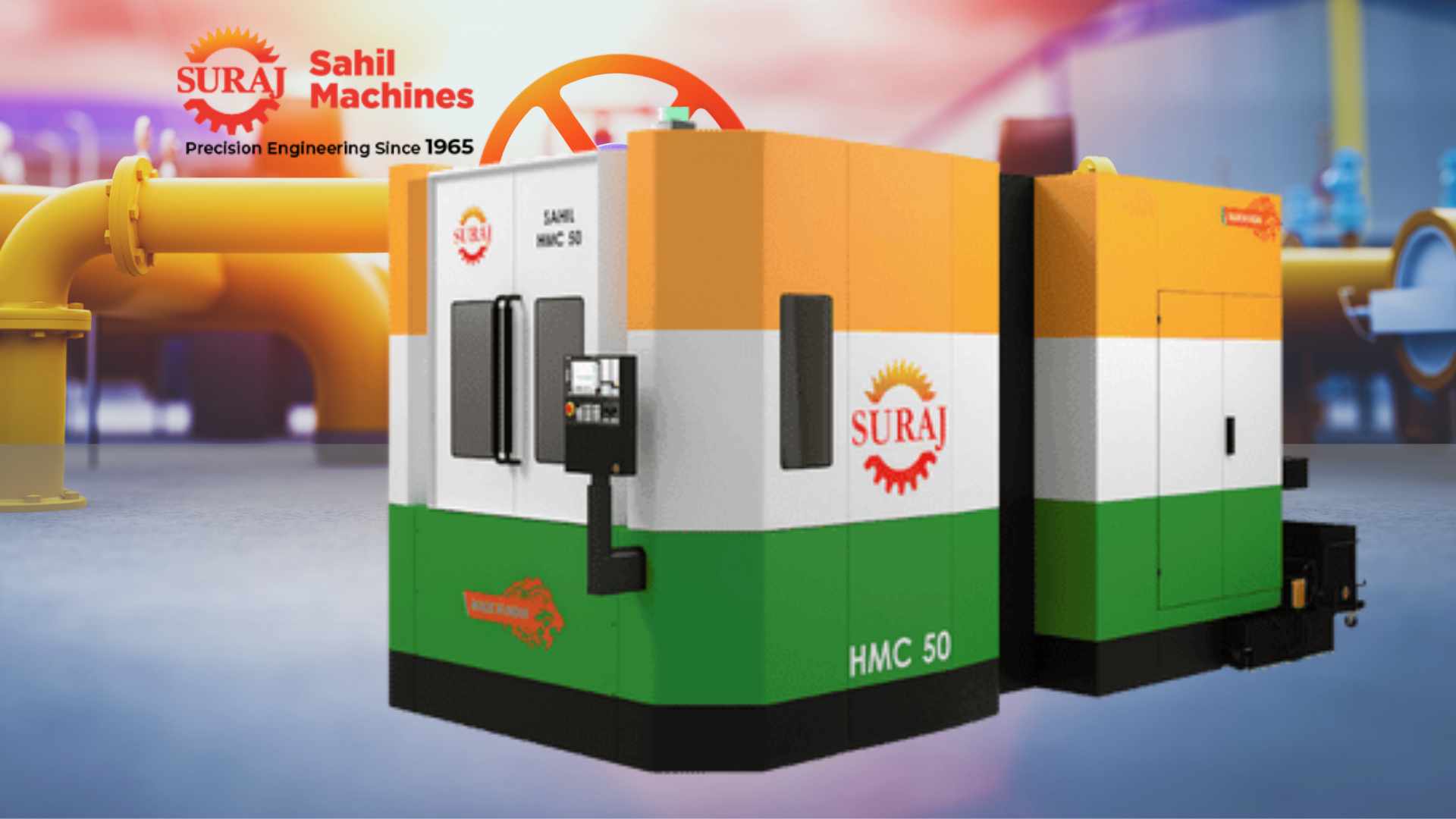
Get in touch with us about anything.
Connect with our team to explore the alloy solutions and machinery expertise you need.