Integrating IoT with CNC Machines: The Future of Smart Manufacturing
The integration of IoT with CNC machining is revolutionizing manufacturing by enabling real-time monitoring, predictive maintenance, and enhanced automation. Discover how smart manufacturing improves efficiency, reduces downtime, and enhances precision in modern CNC operations.
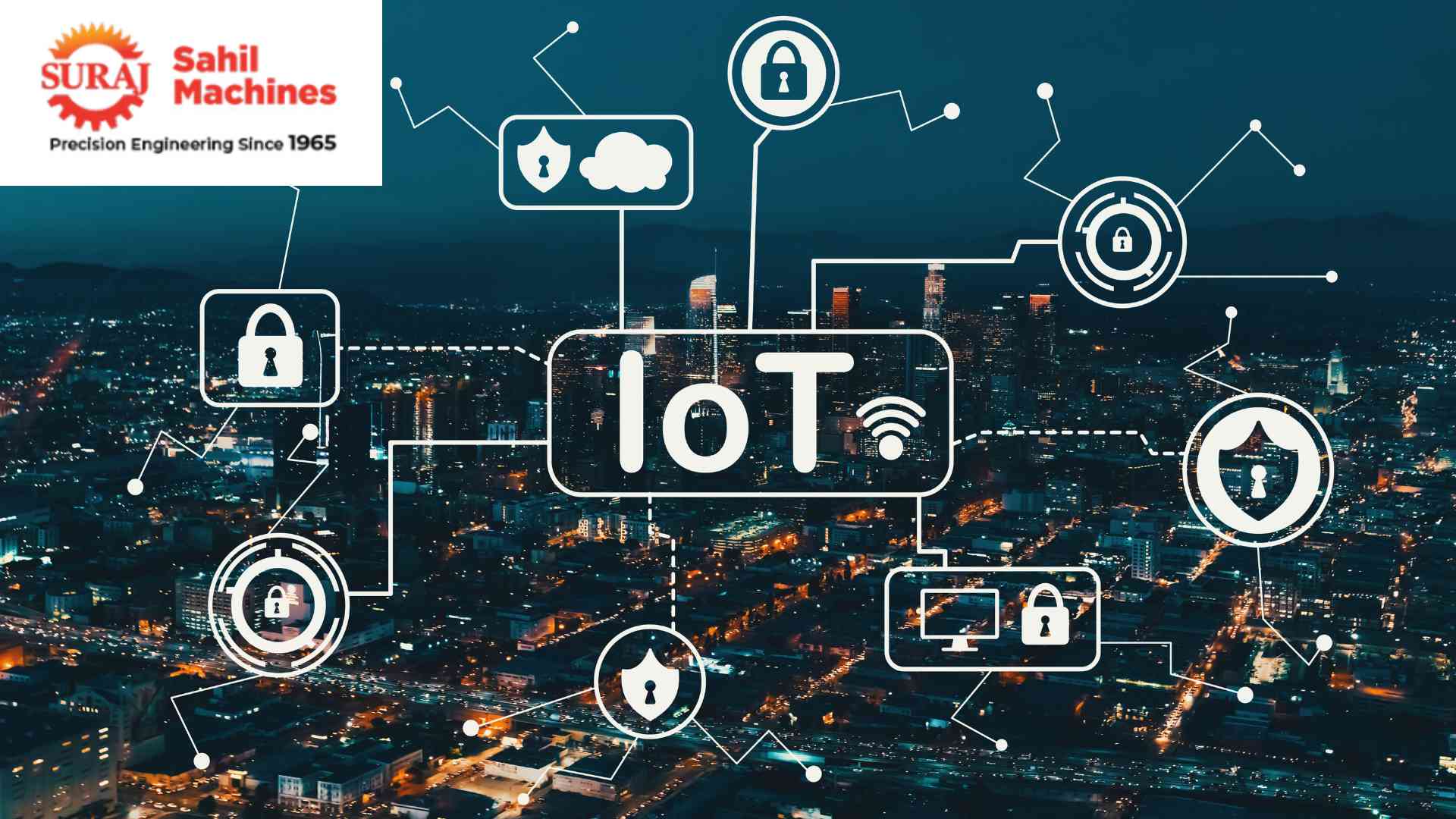
April 01, 2025
Share:
Introduction
The manufacturing industry is undergoing a transformation with the convergence of Computer Numerical Control (CNC) machines and the Internet of Things (IoT). This integration enables unprecedented automation, efficiency, and precision, revolutionizing shop floor operations.
This article explores how IoT is enhancing CNC machining, the key benefits, challenges, and future trends in smart manufacturing.
The Evolution of CNC Machining
CNC machines have long been the backbone of manufacturing, offering high accuracy and repeatability. However, traditional CNC machines operated as standalone units, requiring manual monitoring and servicing.
With IoT, CNC machines are now smart, interconnected systems, capable of real-time data analysis and automated decision-making.
Key Benefits of IoT-Enabled CNC Machines
Real-Time Monitoring & Analytics
IoT sensors collect and analyze extensive operational data, ensuring continuous monitoring and improved performance.
Parameter Category | Metrics Tracked | Benefits |
---|---|---|
Spindle Speed & Temperature | Optimal operating conditions | Increased efficiency |
Tool Management | Wear patterns, performance metrics | Extended tool life |
Energy Management | Power usage patterns | Reduced operational costs |
Quality Control | Vibration patterns, output rates | Higher precision & quality |
Process Efficiency | Output rates, quality measures | Enhanced productivity |
Predictive Maintenance
IoT integration enables predictive maintenance, preventing unexpected breakdowns and reducing downtime.
Maintenance Aspect | Implementation | Result |
---|---|---|
Equipment Monitoring | Continuous trend analysis | Early issue detection |
Maintenance Scheduling | AI-powered scheduling | Maximized uptime |
Equipment Longevity | Preventive maintenance | Longer machine lifespan |
Downtime Management | Predictive analysis | Fewer unexpected stoppages |
Cost Optimization | Data-driven maintenance | Reduced expenses |
Enhanced Quality Control
IoT-driven real-time monitoring ensures superior quality standards by allowing instant adjustments and automated corrections.
Control Measure | Capability | Impact |
---|---|---|
Dimensional Monitoring | Instantaneous measurement | Immediate adjustments |
Parameter Adjustment | Automated corrections | Consistent quality |
Quality Verification | Continuous checking | Reduced defects |
Process Control | Statistical analysis | Higher yield & efficiency |
Implementation Challenges and Solutions
Security Considerations
Security Aspect | Challenge | Solution |
---|---|---|
Data Protection | Cyber threats | End-to-end encryption |
System Access | Unauthorized entry | Multi-factor authentication |
Network Security | Vulnerabilities | Segmented network monitoring |
Integration with Existing Systems
Challenge | Solution | Strategy |
---|---|---|
Hardware Compatibility | IoT sensor retrofitting | Phased installation |
Data Processing | Edge computing solutions | Distributed architecture |
System Communication | Middleware integration | Custom protocols |
Performance Optimization | Gradual upgrades | Continuous assessment |
Future Trends and Possibilities
AI and Machine Learning Integration
The combination of AI and IoT-enabled CNC systems offers:
- Autonomous parameter tuning
- Self-correcting machining
- Advanced quality control through pattern recognition
- Automated workflow management
- Predictive maintenance analytics
Digital Twin Technology
Digital twins create a virtual replica of CNC machines, enabling:
- Real-time process simulation
- Virtual machine testing and optimization
- Enhanced operator training
- Advanced troubleshooting
Implementation Best Practices
Phased Implementation Strategy
Phase | Focus Area | Key Activities |
---|---|---|
Planning | Assessment | Infrastructure analysis, goal setting |
Pilot | Small-scale deployment | Data collection, performance analysis |
Evaluation | Data assessment | ROI calculation, process improvement |
Scaling | Full-scale integration | Gradual expansion to all systems |
ROI and Financial Considerations
Metric | Typical Improvement | Timeline |
---|---|---|
Maintenance Costs | 20-30% reduction | 12-18 months |
Machine Productivity | 15-25% improvement | 6-12 months |
Energy Consumption | 10-20% reduction | 12 months |
Unplanned Downtime | 30-40% reduction | 12-24 months |
Training Requirements
Role | Training Duration | Focus Areas |
---|---|---|
Operators | 2-4 weeks | System operation, basic maintenance |
Maintenance Staff | 4-8 weeks | Advanced troubleshooting, predictive maintenance |
Supervisors | 3-5 weeks | Data analysis, system optimization |
IT Staff | 6-8 weeks | Security, system integration |
Conclusion
The integration of IoT with CNC machining is not just a technological upgrade—it represents a fundamental shift in manufacturing. Companies that strategically implement IoT solutions will achieve higher productivity, improved quality, and reduced costs.
As smart manufacturing continues to evolve, IoT-enabled CNC machines will offer significant competitive advantages in terms of innovation, efficiency, and automation. Businesses that embrace and adapt to these technologies today will thrive in the future of digital manufacturing.
Related Resources
For more insights, visit our CNC Machining Blog!
FAQ
IoT enhances CNC machining by enabling real-time monitoring, predictive maintenance, and automated decision-making, resulting in higher efficiency, reduced downtime, and improved precision in manufacturing.
IoT-powered CNC machines offer real-time data analytics, predictive maintenance, energy optimization, enhanced quality control, and seamless automation, helping manufacturers reduce costs and improve productivity.
Common challenges include data security concerns, system compatibility, high initial investment, and network vulnerabilities. These can be mitigated through end-to-end encryption, phased implementation, and AI-driven monitoring.
What role does predictive maintenance play in IoT-enabled CNC machines?
The future of IoT in CNC includes AI-driven automation, digital twin technology, self-optimizing machines, and energy-efficient smart factories, leading to smarter, more sustainable, and highly efficient manufacturing.
Follow Us:
Latest Posts
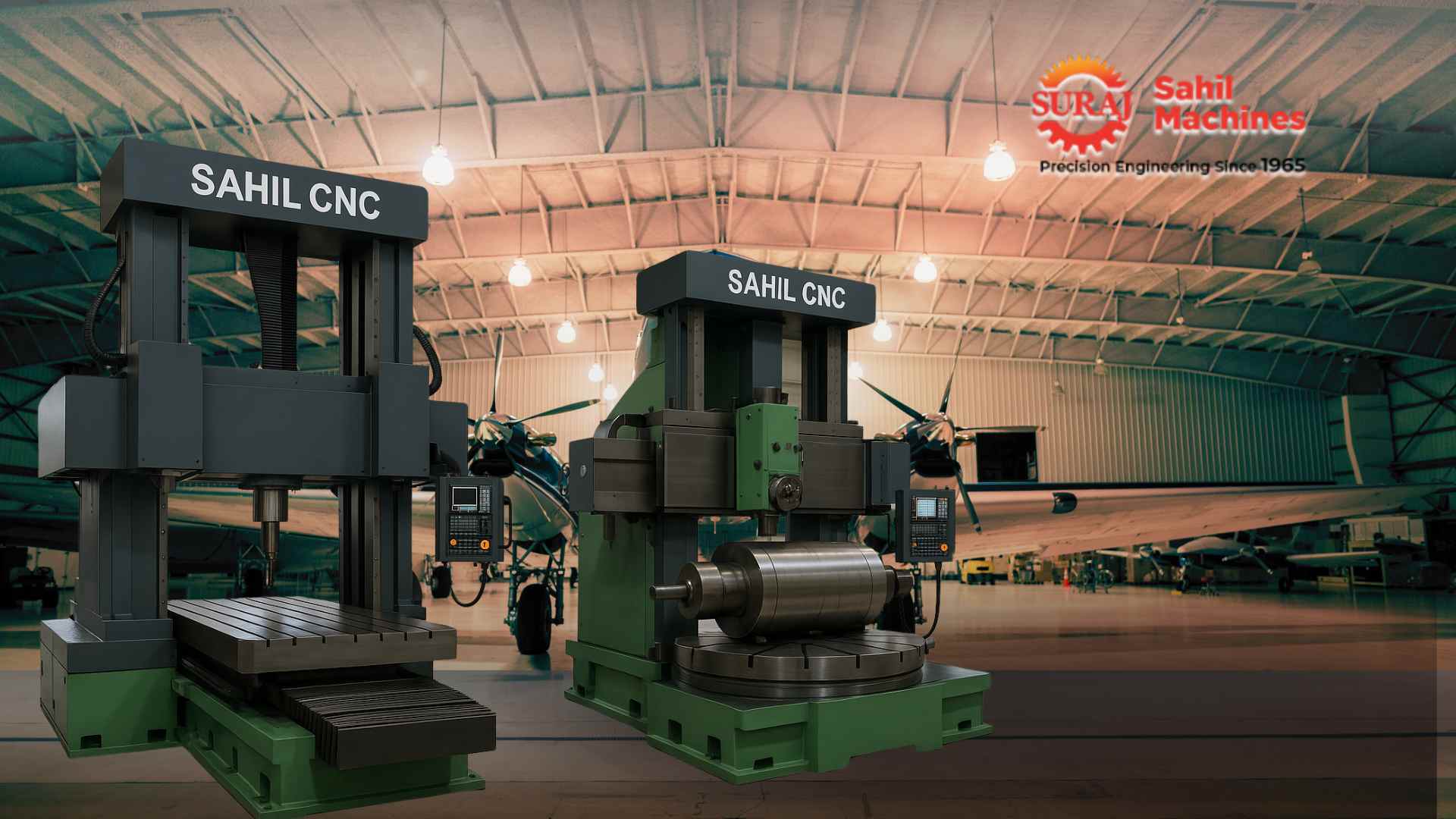
Revolutionizing Heavy Engineering: How Sahil CNC’s Double Column Milling and VTL Machines Transformed Large-Scale Manufacturing
by Admin - April 9, 2025
Get in touch with us about anything.
Connect with our team to explore the alloy solutions and machinery expertise you need.