Implementing Automation in CNC Workshops: Benefits and Challenges
Automation in CNC workshops is reshaping the manufacturing landscape by improving efficiency, precision, and safety. This blog explores the key benefits, challenges, and industry applications of CNC automation.

April 09, 2025
Share:
Introduction
The manufacturing industry is continuously evolving, with automation becoming a key driver of efficiency and productivity. In CNC (Computer Numerical Control) workshops, automation is transforming traditional machining processes by reducing human intervention, increasing production speed, and enhancing precision. As industries strive for higher efficiency and profitability, automated CNC systems have become a cornerstone of modern manufacturing.
Automation in CNC workshops involves integrating robotic arms, automated tool changers, pallet changers, and AI-powered monitoring systems to streamline production. While automation offers substantial benefits such as improved accuracy, reduced labor costs, and higher output, it also presents challenges, including high initial investment, complex integration processes, and the need for skilled labor.
In this blog, we will explore the benefits and challenges of implementing automation in CNC workshops, along with insights into its applications and future trends.
Understanding CNC Automation
CNC automation refers to the use of machines, robots, and software to perform machining operations with minimal human involvement. It involves:
- Automated Loading and Unloading: Robots or automated loaders place raw materials into the machine and remove finished parts, reducing manual handling.
- Automatic Tool Changers (ATC): These systems switch between different cutting tools automatically, minimizing downtime.
- Pallet Changers: Automated pallet systems allow the machine to continue operating while new material is loaded onto another pallet, enhancing production efficiency.
- Real-Time Monitoring and Control: Advanced CNC systems use IoT and AI for real-time monitoring, enabling predictive maintenance and quality control.
- Lights-Out Manufacturing: With full automation, CNC workshops can operate 24/7 without human supervision, boosting productivity.
Benefits of Automation in CNC Workshops
Automating CNC workshops offers several advantages, including improved efficiency, consistency, and cost-effectiveness. Here’s a closer look at the key benefits:
1. Enhanced Productivity and Efficiency
Automation significantly increases the productivity of CNC workshops by reducing cycle times and minimizing idle periods. Robotic loaders and pallet changers enable continuous machining, even during off-hours. With fewer manual interventions, the machines can produce more parts in less time, boosting overall efficiency.
Example:
An automotive manufacturer implementing automated CNC systems can run machines overnight without human supervision, effectively doubling the production output.
2. Improved Precision and Consistency
Automated CNC machines deliver higher precision and consistency compared to manual operations. Robots and automated systems execute tasks with minimal deviation, ensuring uniformity in part dimensions and quality. This is particularly beneficial in industries where tight tolerances are required, such as aerospace and medical manufacturing.
Example:
In medical device manufacturing, automated CNC machines can create precision parts with tolerances as low as ±0.001 mm, ensuring consistent quality across large batches.
3. Reduced Labor Costs and Human Error
By automating repetitive and labor-intensive tasks, CNC workshops can cut down on labor costs. Fewer operators are needed to manage the machines, reducing overhead expenses. Additionally, automation minimizes the risk of human error, resulting in fewer defective parts and less material waste.
Example:
A CNC workshop using robotic arms for material loading reduces its labor requirements by 30-40%, leading to significant cost savings.
4. Enhanced Safety
CNC machining involves rotating tools, sharp edges, and heavy materials, posing potential safety risks. Automation reduces direct human interaction with machines, minimizing the likelihood of accidents and injuries. Automated systems can handle hazardous materials or heavy parts safely, protecting workers.
5. Faster Turnaround and Shorter Lead Times
Automated CNC workshops offer faster turnaround times by optimizing machining processes. Automated tool changers and pallet systems reduce downtime between operations, enabling continuous production. This is particularly advantageous for manufacturers dealing with tight deadlines and high-volume orders.
Example:
An electronics manufacturer using automated CNC machines can reduce lead times by up to 50%, enabling faster delivery to clients.
6. Real-Time Monitoring and Predictive Maintenance
Automation enables real-time monitoring of CNC machines through IoT and AI-based systems. This allows operators to track machine performance, detect issues early, and schedule maintenance proactively. Predictive maintenance reduces unexpected downtime and extends machine lifespan.
Challenges of CNC Automation
While CNC automation offers numerous benefits, it also presents several challenges that manufacturers must address.
1. High Initial Investment
One of the biggest barriers to CNC automation is the substantial upfront cost. Integrating robots, automated loaders, and AI monitoring systems requires significant capital expenditure. Small and medium-sized workshops may find it difficult to justify the investment, especially if they have low production volumes.
Solution:
To overcome this challenge, manufacturers can start with partial automation, focusing on specific repetitive tasks before expanding automation across the workshop.
2. Integration Complexity
Implementing automation in CNC workshops involves complex system integration and programming. Synchronizing robots, CNC machines, and monitoring systems requires expertise and careful calibration. Improper integration can lead to inefficiencies and operational disruptions.
Solution:
Manufacturers can collaborate with automation experts or system integrators to ensure seamless integration and minimize downtime.
3. Workforce Skill Gaps
While automation reduces the need for manual labor, it increases the demand for skilled CNC operators and programmers. Workers need to be trained in operating and troubleshooting automated systems. The skill gap in the manufacturing industry can hinder the effective adoption of automation.
Solution:
Investing in training programs and certifications can help workers acquire the necessary skills to manage CNC automation effectively.
4. Maintenance and Downtime
Automated CNC systems require regular maintenance to prevent malfunctions. While predictive maintenance reduces unexpected downtime, occasional system failures or software glitches can still occur, disrupting production.
Solution:
Implementing redundancy systems and predictive maintenance protocols helps minimize unplanned downtime.
5. Limited Flexibility for Low-Volume Production
Automation is most beneficial for high-volume production. For workshops handling low-volume or custom parts, the return on investment may be lower. Automated systems may also struggle with frequently changing part designs, limiting flexibility.
Solution:
Using modular automation systems allows workshops to scale up or down based on production needs, making automation feasible even for smaller operations.
Applications of CNC Automation
Automated CNC workshops are widely used across various industries:
- Aerospace: Automated CNC machining produces complex, high-precision components with consistent quality.
- Automotive: CNC automation enables mass production of engine parts, gears, and brake components with minimal manual intervention.
- Medical: Automated CNC machines produce surgical instruments and implants with high accuracy.
- Electronics: Automation facilitates large-scale production of PCBs and casings, ensuring consistent quality.
Conclusion
CNC automation is revolutionizing modern manufacturing by boosting productivity, enhancing precision, and reducing costs. Despite challenges such as high initial investments and complex integration, the long-term benefits make automation a worthwhile investment for CNC workshops. As technology continues to evolve, the adoption of AI, robotics, and real-time monitoring will further enhance the efficiency and reliability of automated CNC operations.
Related Resources
FAQ
CNC automation involves using robotic systems, AI, and automated processes to minimize human intervention in CNC machining operations.
Benefits include higher productivity, improved precision, reduced labor costs, enhanced safety, and faster turnaround times.
Challenges include high initial investment, complex integration, workforce skill gaps, and maintenance requirements.
Automation includes robotic loaders, automatic tool changers, pallet changers, and real-time monitoring systems.
Yes, but smaller workshops may start with partial automation and gradually expand based on their production volume and budget.
Follow Us:
Latest Posts
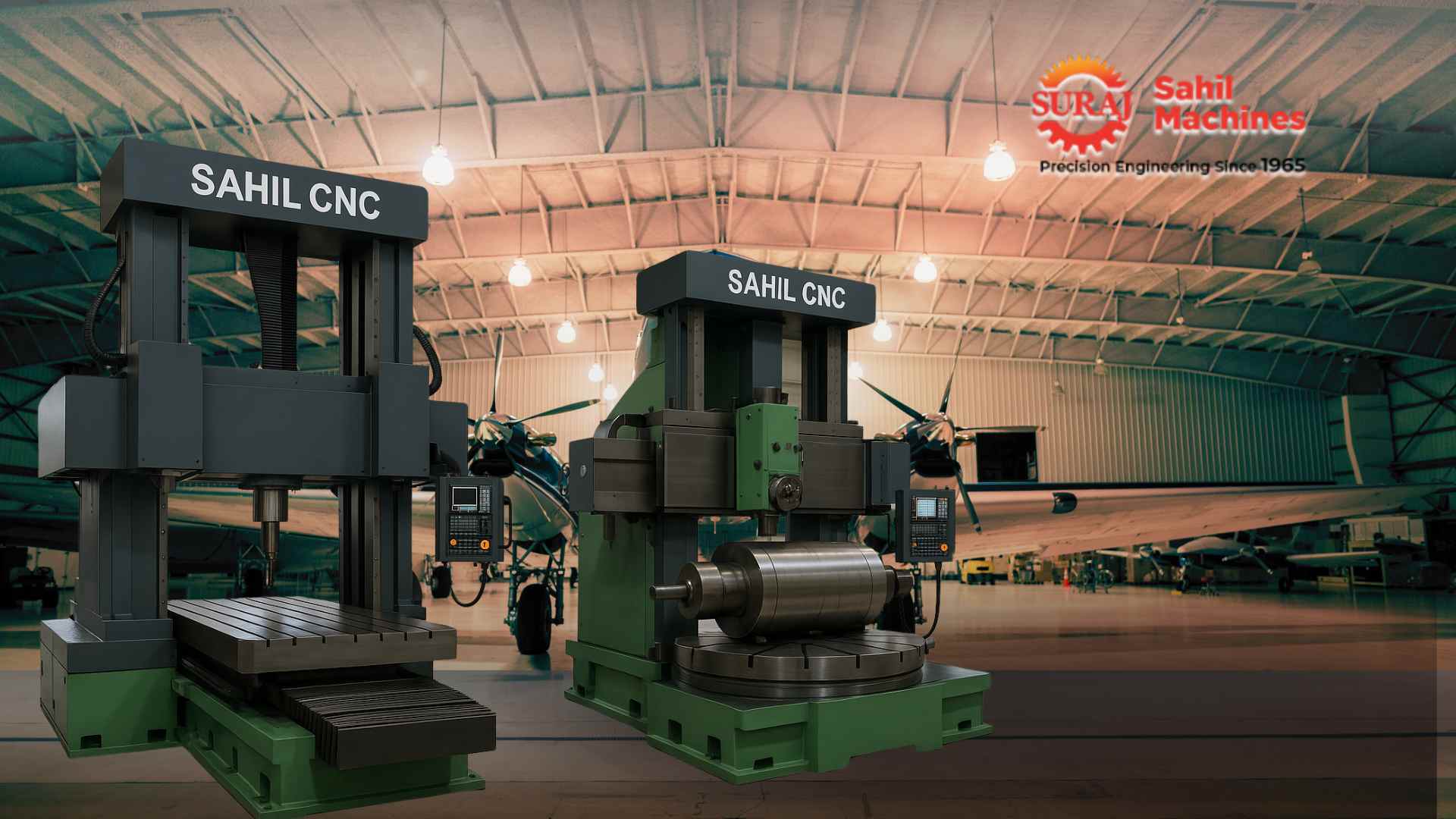
Revolutionizing Heavy Engineering: How Sahil CNC’s Double Column Milling and VTL Machines Transformed Large-Scale Manufacturing
by Admin - April 9, 2025
Get in touch with us about anything.
Connect with our team to explore the alloy solutions and machinery expertise you need.