The Role of Conventional Oil Country Lathes in the Oil and Gas Industry
Discover how conventional oil country lathes play a crucial role in the oil and gas industry by enabling heavy-duty threading, machining, and repair of large-diameter pipes and components.
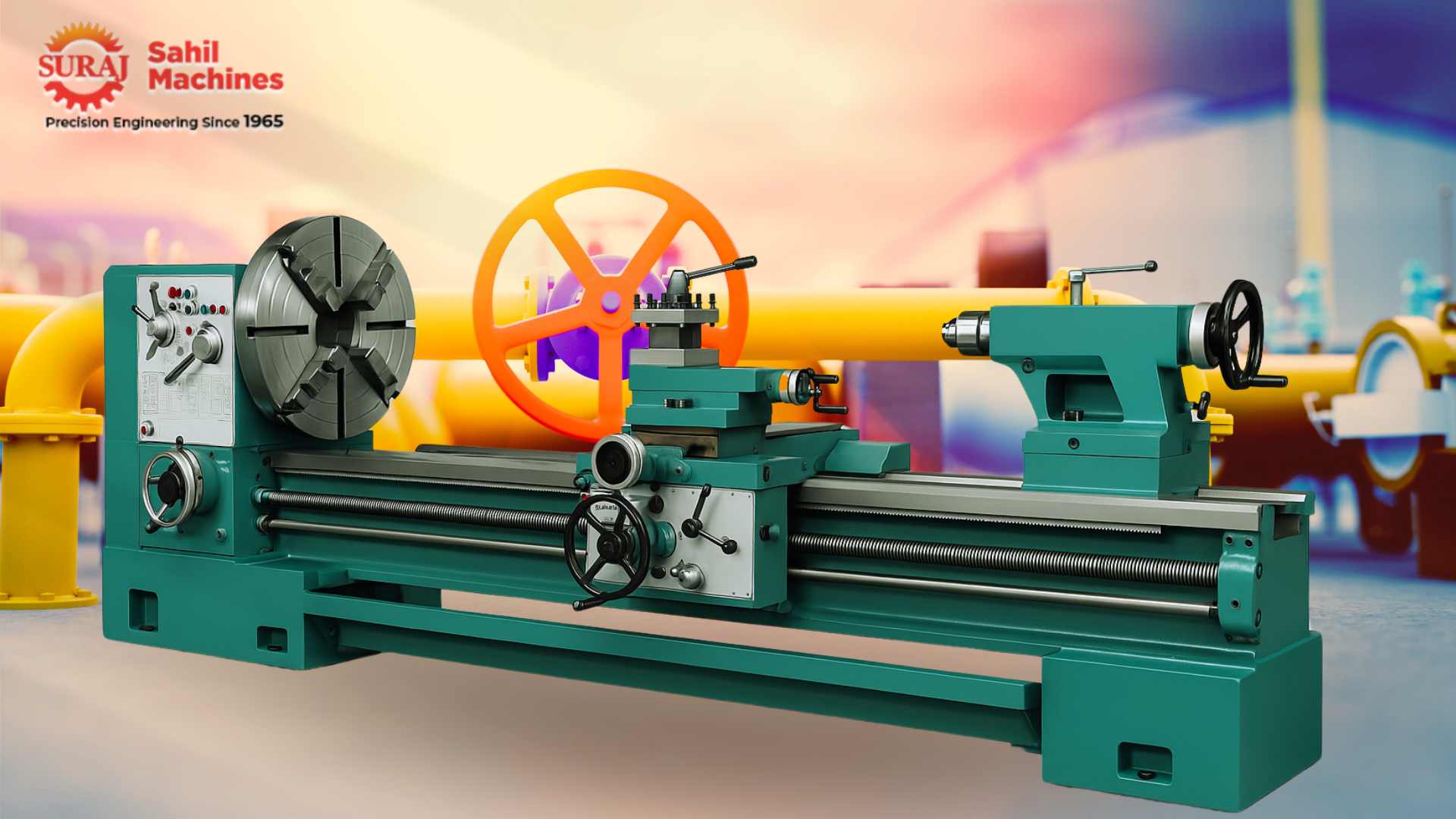
April 02, 2025
Share:
Introduction
The oil and gas industry relies heavily on precision machining to manufacture, maintain, and repair equipment used in drilling and extraction. One of the most essential machine tools in this sector is the conventional oil country lathe. These specialized lathes are designed to handle large-diameter pipes, drill collars, casings, and other critical components used in drilling operations.
Despite the advent of CNC technology, conventional oil country lathes remain indispensable due to their robustness, simplicity, and cost-effectiveness.
This article explores the role of conventional oil country lathes in the oil and gas industry, highlighting their applications, benefits, and continued relevance.
What is a Conventional Oil Country Lathe?
A conventional oil country lathe is a heavy-duty lathe specifically designed to machine large-diameter workpieces, such as pipes and drill collars used in oilfield operations. These lathes have a wide spindle bore, allowing them to accommodate long, thick-walled tubes and threaded components essential in the industry.
Unlike CNC lathes, conventional lathes are manually operated, providing machinists with full control over the machining process.
Key Features of Oil Country Lathes
- Large spindle bore: Accommodates pipes and tubing of significant diameter.
- Heavy-duty construction: Ensures stability and precision during machining.
- Manual operation: Allows machinists to make real-time adjustments.
- Threading capability: Essential for producing API threads on casings and tubing.
- Multiple speed settings: Enables machining of different materials and sizes.
Applications of Oil Country Lathes in the Oil and Gas Industry
Oil country lathes are used extensively in various stages of oil and gas exploration, drilling, and production. Some of the primary applications include:
1. Threading and Re-threading Pipes
One of the most critical applications of oil country lathes is threading and re-threading pipes used in drilling operations. These lathes can cut precise threads on tubing and casing pipes, ensuring a secure connection between components.
2. Machining Drill Collars and Tool Joints
Drill collars and tool joints require high-precision machining to ensure proper alignment and durability in drilling operations. Oil country lathes help achieve the necessary tolerances and surface finishes.
3. Repairing Worn-Out Components
Oilfield equipment experiences extreme wear and tear. Conventional lathes allow machinists to refurbish and repair worn-out parts, such as stabilizers and couplings, extending their operational life.
4. Manufacturing Custom Oilfield Parts
In some cases, standard parts may not be suitable for specific drilling conditions. Oil country lathes enable the production of custom parts tailored to unique drilling requirements.
5. Refacing Flanges and Connections
Flanges and pipe connections must be precisely machined to ensure a leak-proof seal. Oil country lathes are ideal for refacing these components, ensuring they meet industry standards.
Benefits of Using Conventional Oil Country Lathes
Despite advancements in CNC technology, conventional oil country lathes continue to be widely used due to several key advantages:
1. Cost-Effectiveness
Conventional lathes are more affordable than CNC machines, making them an excellent choice for small and medium-sized machine shops serving the oil and gas sector.
2. Simplicity and Flexibility
These lathes are manually operated, giving machinists full control over machining operations. This flexibility is particularly useful for one-off or custom jobs.
3. High Torque for Heavy-Duty Machining
Oil country lathes are designed for heavy-duty applications, providing the necessary torque to machine large and tough materials.
4. Quick Setup and Operation
Unlike CNC machines, conventional lathes do not require extensive programming. This allows machinists to quickly set up and execute jobs, improving productivity.
5. Longevity and Durability
These lathes are built to withstand harsh industrial environments, ensuring long service life with minimal maintenance.
Challenges and Limitations
While conventional oil country lathes offer numerous benefits, they also have some limitations:
- Manual operation requires skilled machinists, which can be a challenge given the shortage of experienced workers in the industry.
- Limited automation, leading to lower efficiency compared to CNC machines in high-volume production.
- Higher dependency on operator skill, which can affect consistency in machining quality.
Despite these limitations, conventional oil country lathes remain a valuable asset for many oilfield machining operations.
The Future of Oil Country Lathes
The oil and gas industry continues to evolve, incorporating advanced machining technologies such as CNC and automation. However, conventional oil country lathes are unlikely to become obsolete due to their practicality, reliability, and cost advantages.
In the future, hybrid models combining manual and digital controls may enhance efficiency while retaining the benefits of conventional lathes.
Additionally, with the increasing demand for energy, the need for precision-machined components will continue to rise, ensuring a steady demand for oil country lathes.
Conclusion
Conventional oil country lathes play an indispensable role in the oil and gas industry, handling essential machining tasks such as threading, repairing, and custom part fabrication. Their robustness, cost-effectiveness, and versatility make them a preferred choice for many machine shops.
While CNC technology has gained popularity, conventional lathes remain vital for operations requiring manual control and high torque.
As the oil and gas sector continues to expand, conventional oil country lathes will remain a key component in ensuring the reliability and efficiency of drilling equipment. By combining traditional machining techniques with modern enhancements, these lathes will continue to serve the industry for years to come.
Explore Related Machines from Sahil Machines:
FAQ
Oil country lathes are specifically designed for machining large-diameter pipes and oilfield components, featuring a larger spindle bore and heavy-duty construction compared to regular lathes.
Despite the rise of CNC technology, conventional lathes remain popular due to their cost-effectiveness, simplicity, and ability to handle heavy-duty machining tasks.
Yes, these lathes can machine various materials, including stainless steel, aluminum, and alloys used in oilfield equipment
These lathes are equipped with threading capabilities to create precise threads on pipes, ensuring a secure and leak-proof connection in drilling operations.
Yes, many small and medium-sized machine shops use conventional oil country lathes due to their affordability and versatility in handling diverse machining tasks.
Follow Us:
Latest Posts
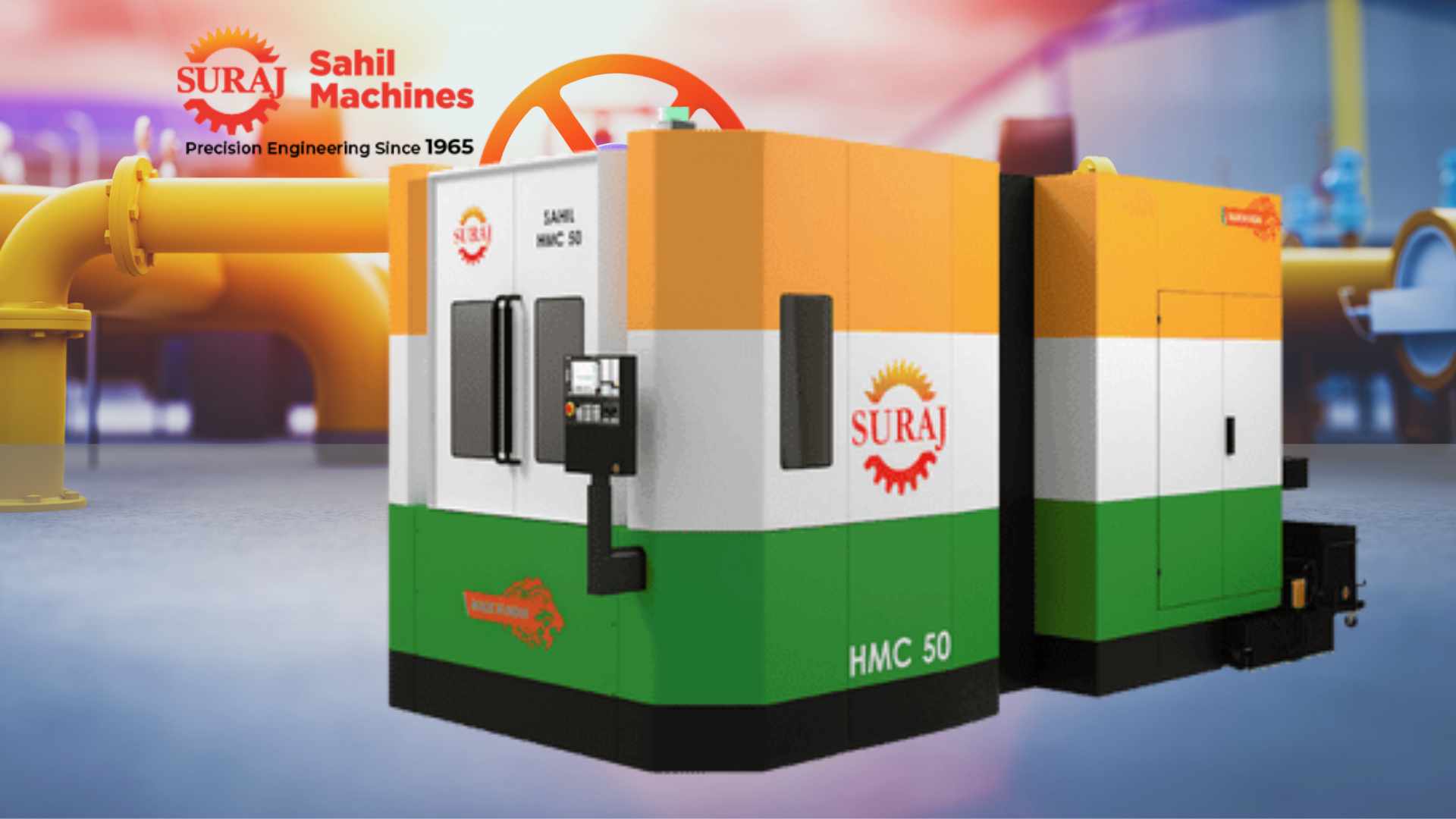
Get in touch with us about anything.
Connect with our team to explore the alloy solutions and machinery expertise you need.