CNC Axle Turning and Burnishing: Revolutionizing Railway Manufacturing
Discover how CNC axle turning and burnishing are transforming railway manufacturing with precision, efficiency, and automation. Learn about their benefits, key features, and best practices for improved production quality and cost-effectiveness.
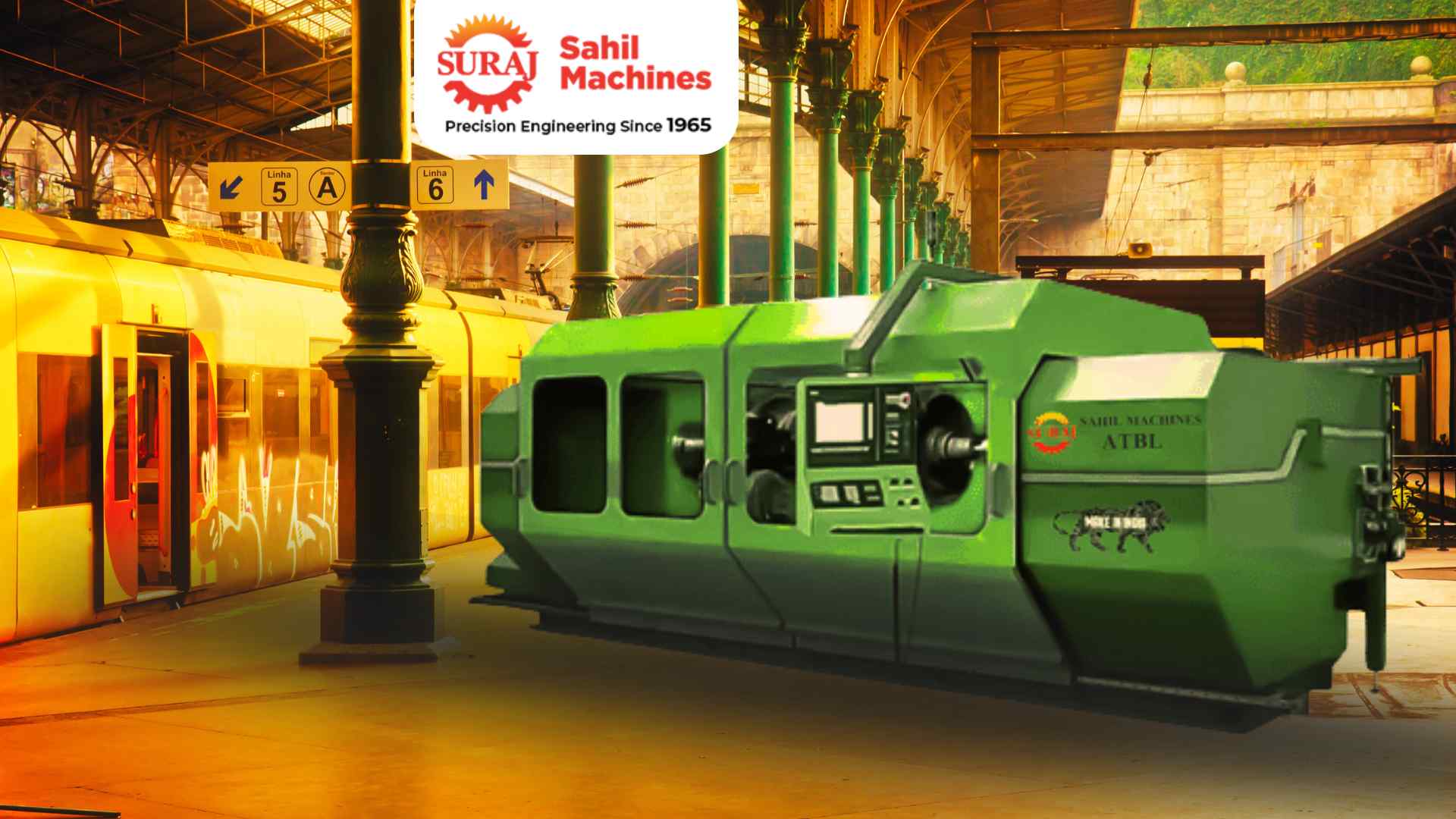
April 01, 2025
Share:
By fully utilizing Computer Numerical Control (CNC) technology, axle production has advanced railway manufacturing to new levels. Axles are the backbone of rail transport, requiring unmatched precision and strength, both of which are now achievable with modern CNC turning and burnishing lathes.
The Evolution of Axle Manufacturing
Historically, axles were manually machined, relying on skilled operators to produce components through labor-intensive processes. This traditional approach led to:
- Variability in quality
- Longer production times
- Greater material waste
With the advent of CNC technology, these challenges have been transformed into precision-driven production, ensuring higher efficiency, consistency, and accuracy.
Understanding CNC Axle Turning: A Deep Dive
CNC axle turning is a state-of-the-art machining process where a workpiece rotates in a CNC-controlled lathe, removing material to achieve precise dimensions. Unlike traditional machining, CNC turning offers:
- Consistent quality across production runs
- Micron-level dimensional accuracy
- Significantly less material waste
- Higher production efficiency
- Minimal human intervention
Discover our CNC turning solutions designed for the railway industry.
The Power of Burnishing in Railway Axle Production
Complementing CNC turning, burnishing is a surface enhancement process where controlled pressure compresses and smoothens the metal surface, offering several advantages:
Surface Enhancement
- Improved surface hardness
- Reduced friction coefficients
- Increased wear resistance
- Enhanced fatigue strength
Performance Enhancement
- Extended service life
- Reduced maintenance requirements
- Higher load-carrying capacity
- Greater operational reliability
Key Advantages of Modern CNC Lathes
The latest CNC axle turning and burnishing lathes offer several advantages, making them indispensable for railway manufacturing:
Precision Manufacturing
- Multi-axis control systems
- Advanced tool positioning
- Real-time measurement & adjustments
- Automated error compensation
Production Efficiency
- Reduced setup times
- Minimal material waste
- Increased production speed
- Ensured consistent quality
Cost-Effectiveness
- Lower labor costs
- Reduced rework requirements
- Improved production throughput
Explore our advanced CNC machining solutions for railway components.
Essential Features of Modern CNC Axle Lathes
When comparing CNC axle turning and burnishing lathes, here are some standout features:
Advanced Control Systems
- Multi-axis coordination
- Real-time process monitoring
- Automated tool compensation
- Intelligent error detection
Smart Manufacturing Integration
- IoT connectivity
- Data collection & analysis
- Remote monitoring
- Predictive maintenance
High-Performance Capabilities
- Rapid tool changing
- High-speed machining
- Advanced cooling systems
- Precision measurement tools
Choosing the right CNC machine can be challenging. Contact Sahil Machines for expert guidance.
Real-World Impact: A Case Study in Excellence
A leading railway component manufacturer implemented CNC axle turning & burnishing technology with remarkable results:
Before CNC Implementation:
- Inconsistent product quality
- High rejection rates
- Longer production times
- Significant material waste
After CNC Integration:
- 30% increase in production efficiency
- 50% reduction in defect rates
- Improved product consistency
- Significant cost savings
The Future of CNC in Railway Manufacturing
The future of CNC axle turning and burnishing is bright, with several emerging trends shaping the industry:
AI Integration
- Intelligent tool path optimization
- Automated quality control
- Predictive maintenance
- Real-time process adjustment
Enhanced Automation
- Robotic material handling
- Automated loading/unloading
- Integrated quality inspection
- Streamlined workflow management
Sustainability Initiatives
- Energy-efficient machining
- Reduced material waste
- Eco-friendly cooling systems
- Optimized resource utilization
Best Practices for CNC Implementation
To maximize efficiency and performance, manufacturers should follow these best practices:
Invest in Training
- Operator training programs
- Maintenance staff education
- Software utilization courses
- Safety protocol training
Establish Quality Controls
- Regular calibration checks
- Measurement verification
- Process monitoring
- Documentation & reporting
Implement Maintenance Programs
- Scheduled preventive maintenance
- Performance monitoring
- Regular software updates
- Tool-life management
Making the Transition to CNC Technology
For manufacturers considering CNC axle turning and burnishing, follow these steps:
Assessment Phase
- Evaluate current processes
- Identify areas for improvement
- Define specific requirements
- Calculate potential ROI
Implementation Strategy
- Select appropriate CNC equipment
- Plan installation timeline
- Train staff
- Establish operating protocols
Monitoring & Optimization
- Track performance metrics
- Analyze production data
- Adjust processes as needed
- Continue staff development
Conclusion
CNC axle turning and burnishing lathes are revolutionizing railway manufacturing by delivering precision, consistency, and efficiency. These technologies are not only improving current processes but also laying the foundation for the future.
With ongoing advancements in AI, automation, and sustainability, CNC lathes will continue to evolve, ensuring safer, more reliable railway systems.
Manufacturers looking to stay competitive must invest in CNC axle turning and burnishing technology. The combination of precision, efficiency, and reliability makes these machines essential for achieving manufacturing excellence in the railway sector.
Explore our CNC solutions for railway manufacturing.
For expert guidance on CNC axle turning and burnishing solutions, Contact Sahil Machines today!
FAQ
Burnishing improves surface finish, increases fatigue strength, and enhances durability by reducing surface roughness.
CNC lathes provide high precision, repeatability, and efficiency, reducing manual errors and production time.
Improved accuracy, faster production, reduced waste, and consistent quality.
Yes, modern CNC lathes are programmable to accommodate various axle dimensions and specifications.
Yes, these processes are largely automated, ensuring efficiency, precision, and minimal human intervention.
Follow Us:
Latest Posts
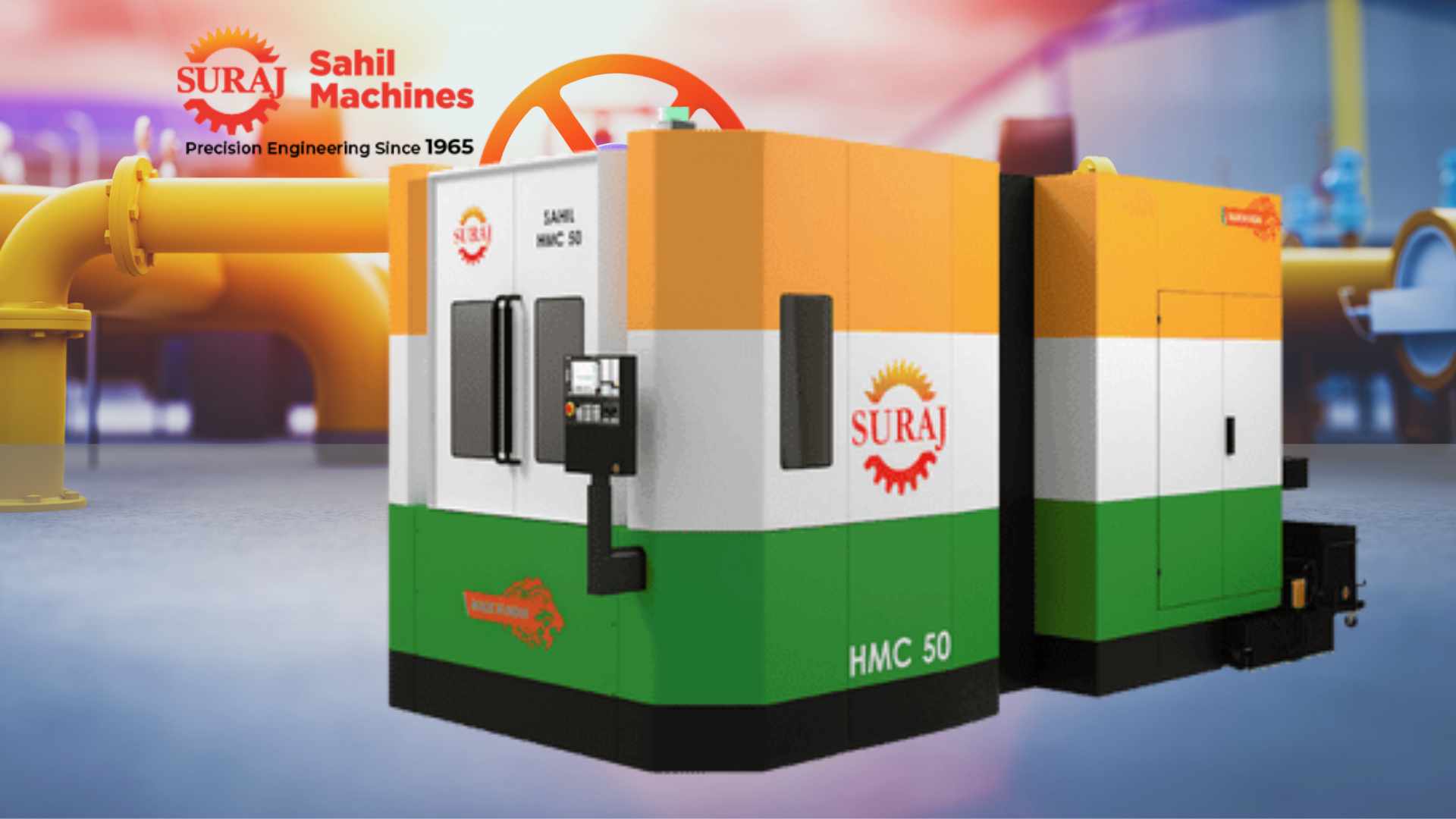
Get in touch with us about anything.
Connect with our team to explore the alloy solutions and machinery expertise you need.