The Essential Role of Cast Iron Floor Plates in Precision Engineering
Cast iron floor plates are essential for precision engineering, offering stability, accuracy, and durability in CNC machining and inspection. They provide superior load-bearing capacity, vibration damping, and wear resistance, making them ideal for automotive, aerospace, and manufacturing industries. With proper maintenance, these plates ensure long-term performance, cost savings, and enhanced productivity in industrial applications.

April 01, 2025
Share:
Cast iron floor plates are vital to precision engineering, offering accuracy, stability, and performance. These components enable industries to achieve the required precision and reliability in manufacturing.
Understanding Cast Iron's Engineering Excellence
Cast iron floor plates represent the peak of material engineering, providing great performance across various manufacturing sectors. Their fundamental characteristics of precision and structural integrity make them indispensable in modern manufacturing.
Key Material Advantages
Exceptional Load-Bearing Capacity
- Supports significant machinery and equipment without structural deformation.
- Maintains even performance under extreme mechanical tension.
Superior Dimensional Stability
- Resistant to changes in shape due to temperature fluctuations.
- Maintains accuracy and prevents dimensional drift.
Advanced Vibration Damping
- Absorbs and distributes mechanical vibrations.
- Ensures precise machining by minimizing micro-vibrations.
Remarkable Wear Resistance
- Highly durable, extending work surface life.
- Minimizes long-term maintenance costs.
Precision Engineering Applications
Machine Tool Industry
In CNC machining, lathing, and milling operations, cast iron plates provide:
- Consistent machining accuracy
- Reduced tool wear
- Improved geometric accuracy of finished parts
Inspection and Metrology
These plates serve as reference surfaces for:
- Flat measurement surfaces
- Minimal measurement uncertainties
- Reliable calibration platforms
Types of Cast Iron Used in CNC Manufacturing
Gray Cast Iron (GCI)
- Contains graphite flakes.
- High wear resistance and vibration damping.
- Used for machine bases, tables, and tool plates.
Ductile Cast Iron (Nodular Iron)
- Contains spherical graphite nodules.
- Higher toughness and impact resistance.
- Used for heavy-duty CNC fixtures.
Meehanite Cast Iron
- A specialized gray iron with controlled microstructure.
- Increased strength and uniformity.
- Common in precision engineering and tooling.
Advanced Manufacturing Sectors
Automotive Engineering
- Enables precise fabrication of engine blocks.
- Ensures accurate transmission part alignment.
- Supports key mechanical structure assembly.
Aerospace Manufacturing
- Facilitates intricate part fabrication.
- Ensures high-precision component positioning.
- Provides reliability in mission-critical systems.
Varieties of Cast Iron Floor Plates
T-Slotted Floor Plates
- Designed for general-purpose workpiece clamping.
- Features slot arrangements for flexible and secure part positioning.
Plain Cast Iron Plates
- Ideal for surface measurement and inspection.
- Provides a high-flatness, obstruction-free surface.
Box-Type Floor Plates
- Robust platforms for large machining operations.
- Offers superior stability for heavy-duty applications.
Benefits of Using Cast Iron Floor Plates in CNC Operations
- Superior Rigidity: Withstands severe machining stresses.
- Enhanced Precision: Ensures dimensional stability.
- Extended Lifespan: Corrosion and abrasion-resistant.
- Cost-Effective: Reduces maintenance and replacement costs.
- Improved Work Safety: Rigid surface prevents workpiece movement.
Maintenance and Longevity
1. Regular Cleaning
- Remove metal shavings, oil, and dust.
- Use non-abrasive cleaning agents.
2. Rust Protection
- Apply anti-rust coatings.
- Store in controlled environments.
3. Flatness Inspection
- Periodically check for distortions.
- Use high-accuracy measuring devices.
4. Load Balancing
- Avoid excessive focal loading.
- Distribute loads evenly to prevent deformation.
Conclusion
Cast iron plates are the foundation of precision engineering, offering stability, durability, and accuracy. Whether for milling, assembly, or inspection, investing in high-quality cast iron floor plates ensures optimal performance, increased productivity, and long-term cost savings.
As manufacturing technology advances, cast iron plates will remain integral to bridging theoretical design with practical execution. They are essential assets in any CNC manufacturing environment.
Related Products
For more details, visit Sahil CNC Machines.
FAQ
Yes, they are a long-term investment for industries that require precision machining and durability. Their longevity and minimal maintenance needs make them cost-effective.
With proper maintenance, cast iron floor plates can last for decades without significant degradation.
They provide a rigid, wear-resistant, and dimensionally stable surface, reducing errors caused by machine vibrations and environmental changes.
Consider factors like load-bearing capacity, size, surface finish, and application type (e.g., machining, inspection, or assembly).
They provide a rigid, wear-resistant, and dimensionally stable surface, reducing errors caused by machine vibrations and environmental changes.
Follow Us:
Latest Posts
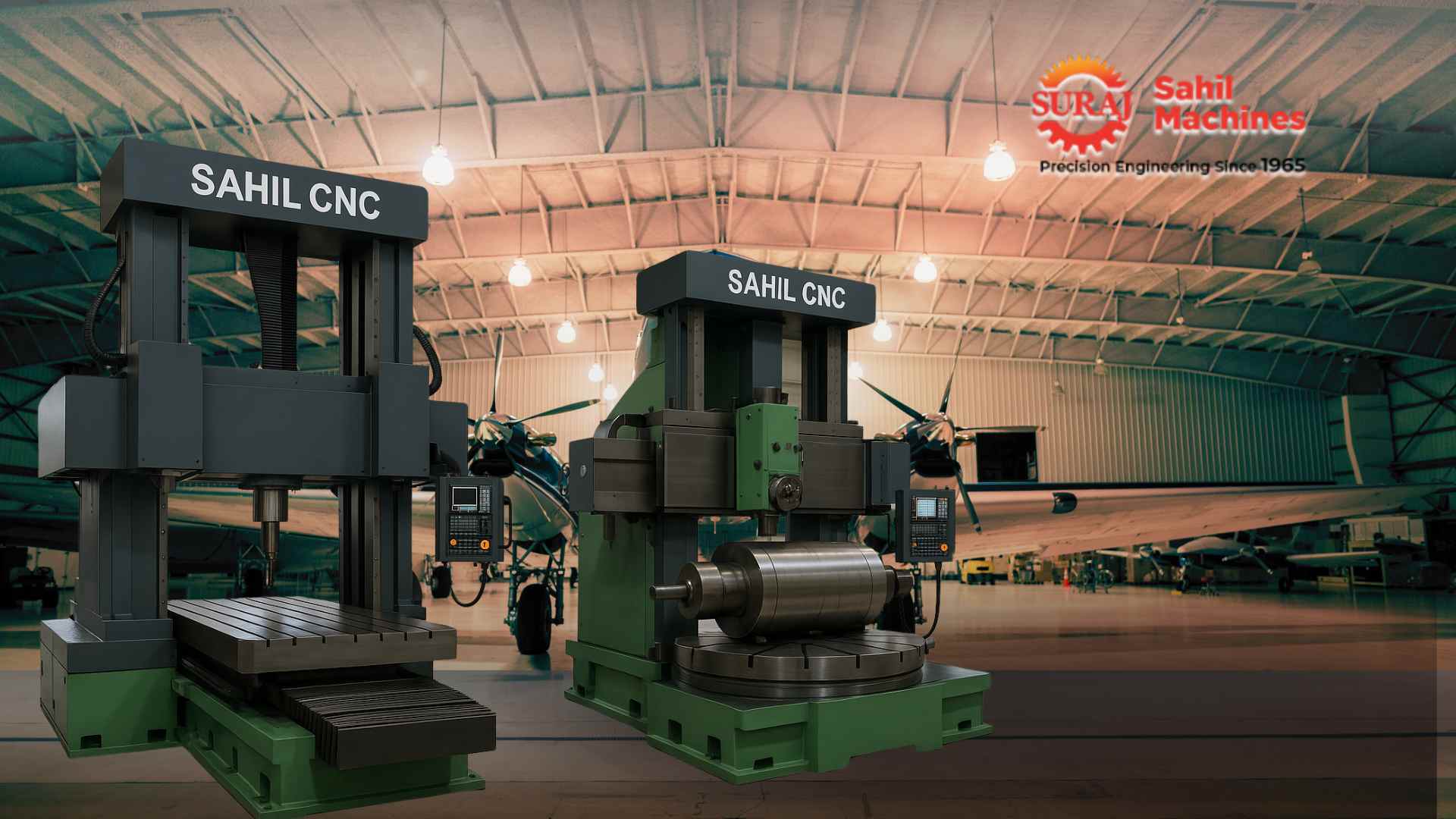
Revolutionizing Heavy Engineering: How Sahil CNC’s Double Column Milling and VTL Machines Transformed Large-Scale Manufacturing
by Admin - April 9, 2025
Get in touch with us about anything.
Connect with our team to explore the alloy solutions and machinery expertise you need.