The Evolution of CNC Manufacturing through CAD/CAM Integration
Explore how CAD/CAM integration, AI-driven optimization, and cloud-based technology are revolutionizing CNC manufacturing by enhancing precision, efficiency, and scalability
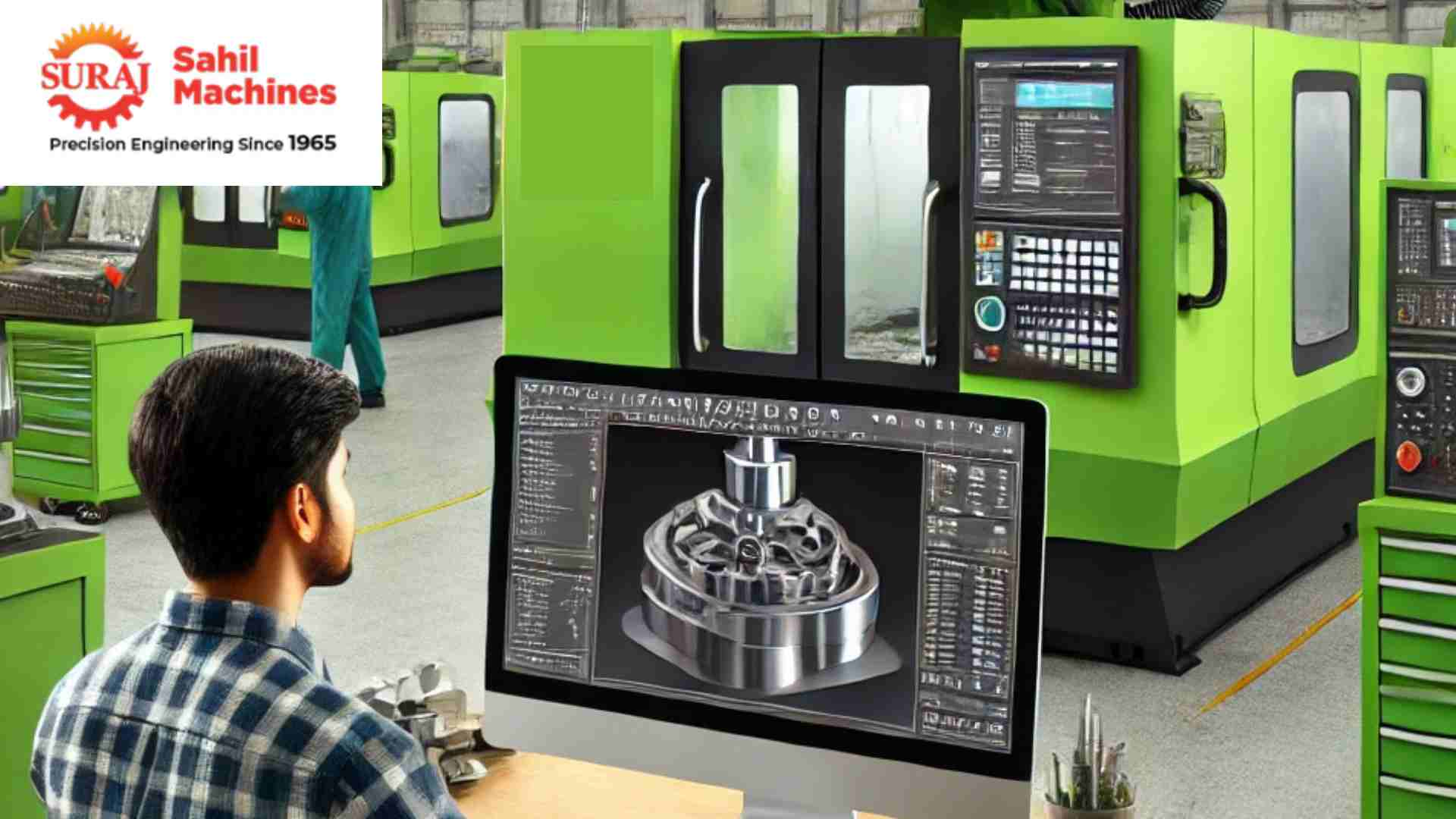
April 01, 2025
Share:
The manufacturing process has evolved immensely with the introduction of CNC machine software. A key driving force behind this evolution is the seamless integration of Computer-Aided Design (CAD) and Computer-Aided Manufacturing (CAM). This integration has revolutionized precision manufacturing, providing unmatched levels of control, productivity, and innovation.
In this post, we will explore how technological advancements, particularly CAD/CAM integration, are transforming CNC manufacturing today. We will also discuss how cloud-based technology, machine learning, and AI-powered features are driving this change.
The Power of CAD/CAM Integration within CNC Manufacturing
1. Seamless Design to Production Workflow
The integration of CAD/CAM software has eliminated the traditional barriers between design and manufacturing. Engineers can now use CAD software to design products and automatically transition them to CAM software, where optimal manufacturing parameters and toolpaths are determined.
- Error Reduction: Eliminates the need for hand-coded programs, reducing errors associated with manual G-code programming.
- Faster Setup Times: Streamlined processes significantly reduce setup times, enabling quicker market entry for products.
2. Enhanced Accuracy and Efficiency
Modern CAD/CAM software is equipped with advanced features that boost productivity and precision in CNC machining.
- Optimal Toolpaths: CAM software calculates the most effective toolpaths, minimizing cutting time and material waste.
- Real-Time Adjustments: Engineers can make instant modifications to designs and manufacturing parameters, ensuring consistent quality and accuracy.
Cloud-Based CAD/CAM Systems: Remote Operations and Team Collaboration
1. Global Cooperation
Cloud-based CAD/CAM platforms enable distributed design teams to collaborate seamlessly, which is crucial in today's global supply chain environment.
- Real-Time Collaboration: Teams can share, comment on, and update designs simultaneously, boosting productivity.
- Remote Manufacturing: CNC machines can be operated remotely, reducing the need for on-site personnel and streamlining global logistics.
2. Scalability and Accessibility
Cloud-based CAD/CAM software is making advanced manufacturing more scalable and cost-effective for businesses of all sizes.
- Cost-Effective: Eliminates the need for expensive on-premise infrastructure, lowering upfront costs.
- Flexibility: Manufacturers can scale operations up or down based on demand, ensuring optimal resource utilization.
Machine Learning and AI-Based Features of CAD/CAM Software
1. Adaptive Optimization of Cutting Parameters
AI-driven CAM programs can automatically adjust cutting parameters like speeds and feed rates based on material properties and tool wear.
- Consistent Quality: Adaptive optimization ensures uniform quality across production runs, minimizing defects.
- Extended Tool Life: AI-based optimization reduces tool wear, leading to lower maintenance costs.
2. Predictive Maintenance Scheduling
Machine learning software can analyze CNC machine data to predict and schedule maintenance activities.
- Reduced Downtime: Predictive maintenance minimizes unexpected breakdowns, improving productivity.
- Cost Savings: Early issue detection helps prevent costly repairs and extends equipment lifespan.
The Future of CAD/CAM Integration in CNC Manufacturing
As technology advances, CAD/CAM integration will continue evolving. Emerging trends include:
- Generative Design: AI-powered generative design optimizes designs based on specific parameters, enhancing efficiency and innovation.
- Digital Twins: Virtual replicas of manufacturing systems enable simulation and process optimization before production begins.
- IoT Integration: CNC machines connected to IoT networks enable real-time monitoring and data-driven decision-making.
Conclusion
The advancements in CNC machine software, particularly CAD/CAM integration, have transformed manufacturing. From streamlined workflows and cloud-based collaboration to AI-driven optimization and predictive maintenance, these technologies are making CNC manufacturing more efficient, precise, and sustainable.
As innovation continues, CAD/CAM systems will unlock new possibilities for manufacturers, helping businesses stay competitive, reduce costs, and deliver high-quality products in a rapidly evolving market.
FAQ
The main advantage is the seamless workflow from design to production. This integration eliminates manual programming errors, reduces setup time by up to 50%, and allows for automatic optimization of manufacturing parameters, resulting in higher precision and efficiency.
Cloud-based solutions provide significant benefits for small manufacturers by eliminating the need for expensive on-premise infrastructure. They offer pay-as-you-go pricing models, require minimal IT support, and enable remote access and collaboration capabilities that were previously only available to larger enterprises.
AI-driven predictive maintenance helps companies save costs by reducing maintenance expenses by 20-30%, cutting unexpected breakdowns by 45-55%, extending machine lifespan by 15-25%, and improving overall productivity by 10-20%. By detecting potential failures early, businesses can minimize downtime, optimize resource usage, and enhance operational efficiency.
Implementing AI-driven predictive maintenance takes around 2-3 months for basic setup and up to 6 months for full integration. Staff training typically requires 2-4 weeks for basic operation, 1-2 months for advanced features, and 3-6 months for complete proficiency. Regular updates and refresher training are recommended to ensure optimal performance.
No, most modern CAD/CAM software is designed to work with existing CNC machines through post-processors. However, older machines (15+ years) might require controller updates or middleware solutions to fully utilize advanced features. A gradual upgrade approach is often recommended to manage costs and minimize disruption.
Follow Us:
Latest Posts
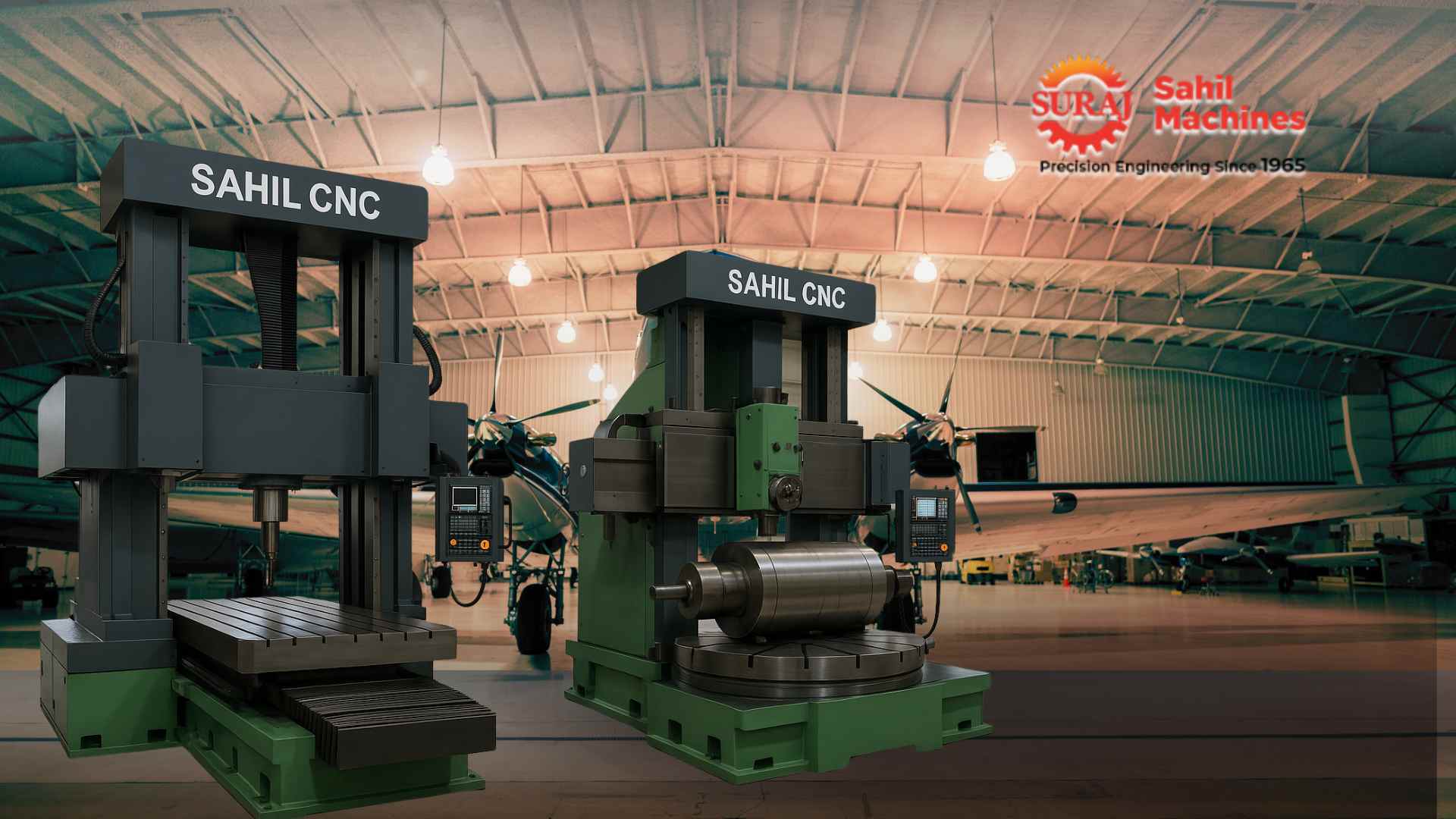
Revolutionizing Heavy Engineering: How Sahil CNC’s Double Column Milling and VTL Machines Transformed Large-Scale Manufacturing
by Admin - April 9, 2025
Get in touch with us about anything.
Connect with our team to explore the alloy solutions and machinery expertise you need.