Understanding Vertical Turning Lathe (VTL) Machines: A Comprehensive Resource for Buyers
The manufacturing sector requires machines with high precision, enhanced productivity, and the ability to perform complex operations. This is where Vertical Turning Lathe (VTL) machines come to the rescue.
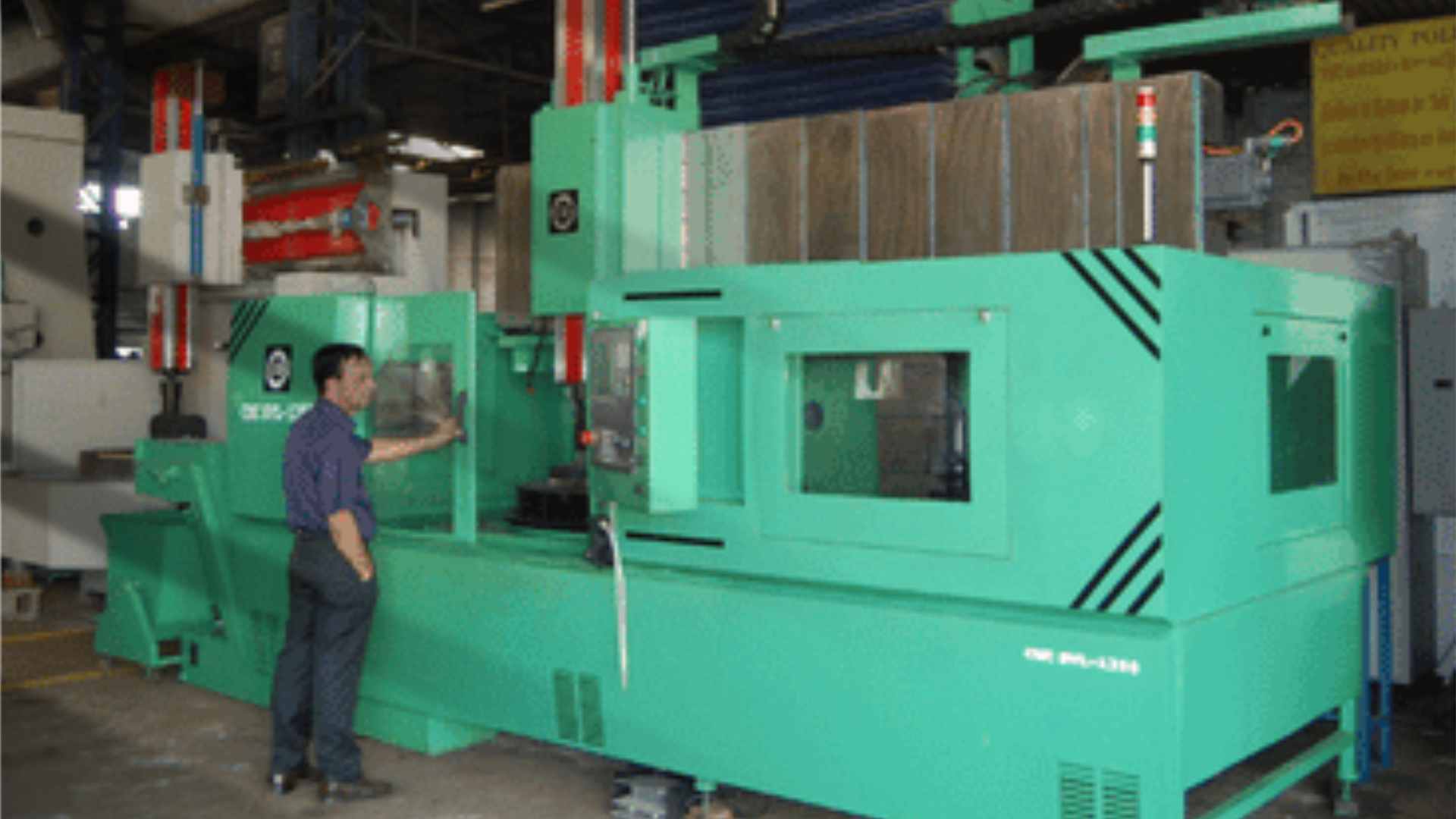
September 12, 2024
Share:
The manufacturing sector requires machines with high precision, enhanced productivity, and the ability to perform complex operations. This is where Vertical Turning Lathe (VTL) machines come to the rescue.
The need for high precision, enhanced productivity, and the ability to perform a variety of operations in modern manufacturing processes has made VTL machines a critical component.
What is a Vertical Turning Lathe (VTL) machine?
VTL (Vertical Turning Lathe) machines are specialized equipment used in the manufacturing industry for machining large, heavy, and complex cylindrical components. Unlike horizontal lathes, VTL machines hold the workpiece vertically, allowing gravity to assist in securing the part, which is particularly useful for heavy items. They perform multiple tasks like turning, boring, drilling, and other operations.
Principles of VTL Machines for Heavy-Duty Manufacturing
The Vertical Design
The workpiece is mounted vertically and utilizes gravity for stabilization. The gravitational assistance reduces the need for clamping systems and is just supported by a rotating table. It is often designed in large diameters to accommodate large workpieces.
Tools and Multi-Axis Movement
The VTL machines are capable of handling multiple tools facilitating multiple complex functions. The cutting tools are mounted on a turret that moves vertically (Z-axis) and horizontally (X-axis).
High Precision and Stability
VTL machines are designed to provide stability while manufacturing larger workpieces. They ensure workpieces are manufactured with high precision and accuracy. They reduce physical strain for a VTL machine operator.
CNC and Automation
CNC programming enables complex machining tasks with high accuracy and repeatability. It also in turn reduces manual intervention and operator errors.
Coolant System and Chip Management
It is equipped efficiently for the removal of metal chips and managing heat further extending the life of the tools and ensuring a smooth operation.
Heavy-Duty Work Handling
VTL machines have a robust frame and are capable of handling large, heavy, and bulky workpieces that are difficult to machine on horizontal lathes. They are designed to perform a range of operations such as turning, facing, boring, grooving, and threading.
Work-holding and Safety Features
VTL machines are integrated with enclosures and safety guards to protect VTL machine operators from debris and coolant splashes. Furthermore, they are equipped with mechanisms to be used in case of emergencies.
Choose the right machine for your industry. Here is a quick look at the different types of VTL machines available in the market.
Types of VTL Machines
VTL machines are designed specifically for various operations. They perform a wide range of tasks like turning, facing, boring, grooving, threading, and complex machining operations on large, heavy, and precision workpieces.
Single Column VTL: A compact design featuring a single column supporting the tool head. It is suitable for machining medium to large-sized workpieces.
Double Column (or Twin Column) VTL: It is designed with two columns to ensure stability and rigidity. It is best suited for very large and heavy workpieces requiring high precision.
Computer Numerical Control (CNC) VTL: It is designed specifically for automation, high-precision, and complex manufacturing. It is widely used in the aerospace and automotive industry.
Manual VTL: It is economical and used for simpler manufacturing functions where CNC control is not required.
Multi-Axis VTL: It is equipped with multiple axes to manufacture complex and intricate parts. It reduces the need for multiple setups in sectors that require complex machining.
Universal VTL: Its versatile design provides solutions for a wide range of machining operations. It is mainly used in environments requiring diverse machining.
Heavy-Duty VTL: It is designed with a robust frame and powerful motors for machining large, heavy, and tough materials. It is widely used in mining and the construction industry for high power and enhanced durability.
Vertical Grinding Lathe: A combination of a grinding spindle and a vertical lathe used for precision grinding operations on large and heavy workpieces.
Vertical Boring and Turning Mill: A combination of a turning mill and a vertical turning lathe used for both boring and turning operations. It reduces the need for multiple machining setups.
Ram Type VTL: It is designed with a sliding horizontal arm and is used for manufacturing workpieces with complex geometries.
Pick-up VTL: It is designed with automation and features a pick-up spindle to reduce manual handling. It is used widely in the automotive industry for improved workflow efficiency.
Let us dive deep into where and how VTL machines are used in heavy-duty manufacturing. Vertical Turning Lathe (VTL) is used in a diverse environment and has various applications. Some of them are:
Aerospace Industry
In the aerospace industry, VTL machines are essential for machining large and complex aircraft engine parts, such as turbine discs and casings. These machines ensure precision and robustness in producing landing gear components, which are critical for the safe and reliable operation of aircraft.
Automotive Industry
VTLs are essential in the automotive industry for manufacturing large brake components like brake discs and drums. They are also used to machine substantial automotive parts such as wheel hubs and rims, ensuring precision and durability in critical vehicle components.
Heavy Machinery Manufacturing
VTL machines are essential in producing large gear blanks for heavy machinery and machining components for construction equipment, such as bearings and housings. These applications ensure robust, precise parts critical for the reliability and performance of industrial and construction machinery.
Energy Sector
VTL machines are essential for the precision machining of large turbine components, crucial for power plants. They also specialize in producing rotor hubs and bearings for wind turbines, ensuring efficient and reliable energy generation. Their capabilities make them indispensable for both traditional and renewable energy sectors.
VTL Machines specializes in machining large valves and flanges for pipelines and equipment, as well as producing essential parts for drilling equipment, such as oversized drill bits and casings. Their precision and capacity make them ideal for handling complex, high-demand components in various industrial applications.
Railway Industry
Vertical Turning Lathe (VTL) machines are crucial for the railway industry, where they are used to machine train wheels for smooth operation and safety. They also produce axle housings and other essential railway components, ensuring durability and precision in critical rail infrastructure.
Marine Industry
VTL (Vertical Turret Lathe) machines are essential in the maritime industry for their capability to handle large-scale machining tasks. They are commonly used to machine propeller shafts, which are crucial for the propulsion of ships and marine vessels. Additionally, VTL machines are instrumental in producing large structural components for ship hulls, ensuring the structural integrity and durability of marine vessels.
VTL machines are crucial for producing missile and rocket components and handling the machining of large, intricate parts with precision. They are also used to manufacture heavy-duty armor plating for military vehicles, ensuring durability and strength in high-stress applications.
General Manufacturing
VTL machines are essential for machining large bearing rings and producing heavy-duty parts like couplings and connectors. These machines excel in handling sizable components, making them ideal for various industrial applications where precision and durability are critical. Their versatility ensures reliability in producing robust industrial equipment.
Mining Industry
VTL Machines excel in machining large parts for excavators and mining equipment, including crucial components for rock crushers and other mining machinery. Their precision and capability ensure high-quality production for robust machinery used in demanding industries.
To enhance your manufacturing sector, you do not look any further. Check out Sahil CNC machines for a diverse range of VMC machines as per your requirements.
Next, let’s look through the workings of a VTL machine for a clear-cut idea of its construction and working.
Components and working of a VTL machine
High-strength materials are typically used in the making of VTLs for accuracy, stability, and longevity during operation. Here’s a quick look at the essential components of a VTL machine:
-
The bed is a stable base for the machine and supports the other components.
-
The vertical column supports the cross rail and cutting tools.
-
The cross rail is a movable horizontal support for the cutting head, allowing vertical adjustment.
-
The turret head holds multiple cutting tools and rotates to bring the desired tool into position.
-
The table or chuck is a large, rotating platform that holds and rotates the workpiece during machining.
-
The spindle drives the chuck/table to rotate the workpiece.
-
The tool post holds and positions the cutting tools during operation.
-
The control panel is an Interface for operating the machine, adjusting settings, and programming CNC operations.
-
The coolant system delivers coolant to the cutting area to reduce heat and extend tool life.
It is usually constructed from premium cast iron or welded steel. It minimizes vibrations, maintains machining accuracy, and ensures stability and rigidity throughout the operation.
A Vertical Turning Lathe (VTL) machine operates by securing a workpiece on a horizontal rotating table, while the cutting tool is mounted on a vertical ram. The moment the table starts spinning, the cutting tool moves along multiple axes to perform precise machining operations such as turning, boring, and facing. The vertical orientation allows for easy handling of large, heavy workpieces, and the robust construction ensures stability and accuracy. The advanced CNC control enables automated and repeatable machining processes, making VTLs essential for producing high-quality components with intricate details.
Advantages of VTL Machines
Precision and Versatility
VTLs offer superior accuracy for complex, large-scale components. Its vertical orientation allows for easy setup and better stability, minimizing deflection during high-speed cutting. This machine adapts to various materials and geometries, making it ideal for diverse industries.
Heavy-duty manufacturing and Durability
Its robust construction makes it easier to handle large and heavy workpieces, VTLs’ rigid build and advanced materials ensure long-term performance, reducing maintenance needs and extending operational life.
Multi-tasking and Efficiency
The Vertical Turning Lathe (VTL)excels in multi-tasking and efficiency by combining several machining operations into a single setup. Its design allows for simultaneous turning, milling, and drilling. This reduces setup times and increases productivity.
Advanced tooling and Automation
Advanced features like CNC controls, automated tool changers, and advanced sensors, reduce manual intervention, improve accuracy, and optimize production rates. Such advancements streamline complex operations, ensuring high-quality results and consistent performance.
Cost-Effectiveness and Reduced Labour
Vertical Turning Lathes (VTL) offer cost-effectiveness and reduced labor by optimizing machining efficiency and minimizing material waste. Their multitasking feature reduces manual interventions. These machines streamline production processes, lowering overall labor costs and enhancing productivity.
Disadvantages of VTL Machines
Maintenance and Cost
VTL machines can be expensive to purchase and set up. Furthermore, timely maintenance is required to ensure the optimal performance of machines.
Complexity and Setup
VTL machines require trained and engineered individuals for operations and programming to make them efficient and faster. The setup and functioning might be time-consuming but is crucial for required results.
**Limited to Vertical Workpiece **
VTL machines are best suited for vertical workpieces, limiting their versatility compared to horizontal lathes. Do your research and select the right machine for your requirements.
Energy Consumption
VTL machines consume a high amount of energy, leading to increased operational costs. Along with the tool cost, maintenance,etc it can be a little heavy on your pockets.
What is to be done, is to be done. Every machine in the manufacturing sector has its pros and cons but when you keenly notice the advantages always override the drawbacks. This is exactly where you need us as well. At Sahil Machines, we brief you clearly and help you choose the best as per your requirements.
Why choose Sahil Machines?
Choosing and selecting the right Vertical Turning Lathe (VTL) as per your needs is all that you want. Well, we want the same, for you to have an efficient, accurate, and fast manufacturing experience.
At Sahil Machines, we ensure you receive top-quality products. Backed by years of industry experience, we offer advanced VTL machines that deliver exceptional precision, reliability, and efficiency, tailored to meet the unique demands of your operations. Sahil Machines offers customizable solutions that meet the diverse requirements of customers across industries.
Vertical Turning Lathe (VTL) machine is an essential tool in contemporary manufacturing, providing unmatched accuracy, effectiveness, and adaptability. They are key to achieving superior manufacturing standards and advancing innovation as industries continue to change and demand ever-more complex and accurate products.
FAQ
Aerospace, automotive, heavy machinery, and energy production industries benefit from VTL machines due to their capability to handle large, heavy components.
VTL machines need significant floor space due to their large size and the required safe operating area around them.
VTL machines offer high precision, efficient machining of large workpieces, and improved productivity for complex components.
They can handle various metals and alloys, though suitability depends on material properties and machining requirements.
VTLs provide superior precision, efficient vertical machining, and robust performance, making them ideal for handling large and complex components in demanding industries.
Follow Us:
Latest Posts
Get in touch with us about anything.
Connect with our team to explore the alloy solutions and machinery expertise you need.