Optimising Aerospace Machining: A Comparative Analysis of Carbide, Ceramic, and PCBN Cutting Inserts
A detailed comparison of cutting insert technologies in aerospace machining, analyzing the performance of carbide (65% market share), ceramic (20%), and PCBN (15%) inserts. The article covers cost-benefit analysis, implementation strategies, and future trends, helping manufacturers optimize their machining operations for better efficiency and precision.
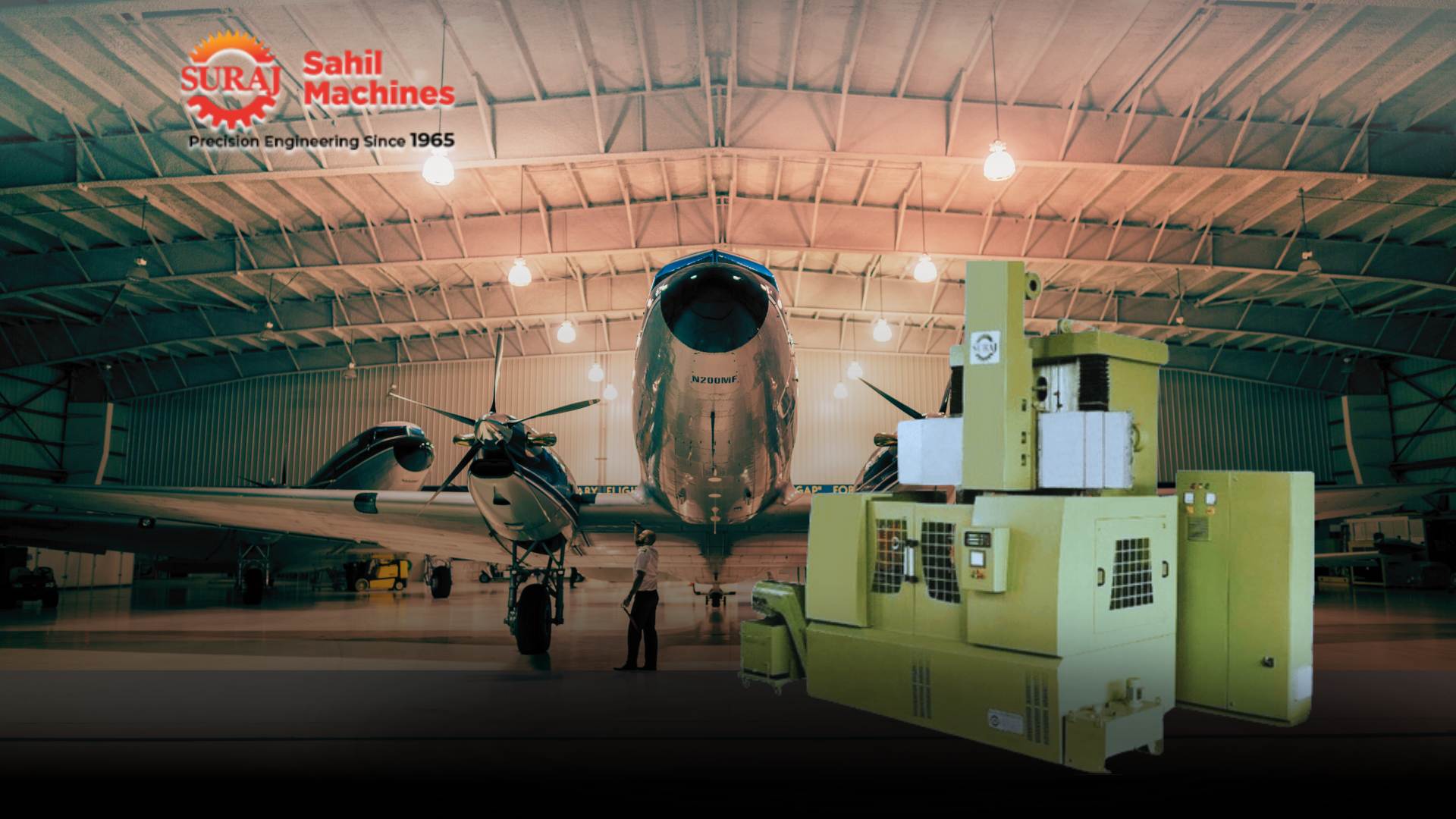
April 01, 2025
Share:
In the $298 billion aerospace machining industry, success often comes down to the smallest details. When manufacturing tolerances call for accuracy to within ±0.0001 inches—about one-fifth the width of a human hair—anything less than the right cutting tool for the job can be the difference between success and disaster.
The Challenge of Modern Aerospace Materials
Today's aerospace components push both structural and material boundaries. Consider titanium alloys: despite their exceptional strength-to-weight ratio properties, they are machined 45% slower than average steel. During machining, temperatures can exceed 800°C, creating challenging conditions where poor cutting tool selection can lead to catastrophic failure. With superalloy material waste reaching up to 25%, selecting the right cutting tool becomes critical for both quality and economics.
The Three Pillars of Cutting Technology
Carbide Inserts: The Industry Backbone
Commanding 65% of aerospace machining operations, carbide inserts have earned their place as the industry's workhorse. At $15-30 per cutting edge, they offer exceptional value while delivering consistent performance. These versatile tools maintain their integrity up to 700°C and achieve surface roughness values between Ra 0.8-3.2 micrometers.
Key performance metrics include:
- Cutting speeds of 60-150 meters per minute for titanium alloys, providing a reliable baseline for standard machining operations
- Sustained performance with 45-60 minutes of continuous cutting capability, making them ideal for longer production runs
- Versatile application range from rough machining to semi-finishing operations, offering excellent value across multiple stages of production
Ceramic Inserts: Masters of Heat
Representing 20% of the market share, ceramic inserts excel when temperatures rise beyond carbide's comfort zone. Though more expensive at $40-80 per cutting edge, their performance in machining nickel-based superalloys justifies the investment. Their capabilities include:
- Impressive cutting speeds of 200-300 meters per minute for superalloys, significantly accelerating production times
- Reliable operational duration of 20-30 minutes, providing consistent performance in high-temperature applications
- Superior surface finish capability down to Ra 0.4 micrometers, ensuring high-quality component production
PCBN Inserts: The Premium Performer
While comprising only 15% of aerospace machining, PCBN Inserts represent cutting-edge technology. Their premium $100-200 per cutting-edge price tag delivers exceptional performance:
- Industry-leading hardness rating of 4500 HV (second only to diamond)
- Superior cutting speeds up to 350 meters per minute on hardened steel
- Extended operational duration of 60-90 minutes
- Unmatched surface finish capability of Ra 0.2 micrometers
Economic Impact and Performance Benefits
While cutting inserts typically represent only 3-5% of total machining costs, their influence extends to 65% of operational expenses. Investment in premium tooling yields substantial returns:
- 30-50% reduction in machining costs
- 40-60% improvement in productivity
- 25-35% reduction in quality issues
- 45-65% extension in tool life
Optimizing Insert Selection for Specific Applications
Titanium Alloy Machining
Success in titanium alloy machining requires:
- Implementation of carbide inserts with sharp cutting edges to minimize cutting forces
- Strategic selection of positive rake angles for optimal heat management
- Deployment of rigid toolholding systems to eliminate vibration and ensure precision
Superalloy Machining
For heat-resistant superalloys, consider:
- Utilizing ceramic inserts for high-speed machining operations
- Implementing PCBN inserts when superior surface finish is required
- Employing round insert geometries to maximize tool life and performance
The Future of Aerospace Machining
The cutting tools market in aerospace continues to grow at a 5.8% CAGR (2024-2029). Recent technological developments have yielded:
- Coating improvements delivering 35% performance enhancements
- AI-driven wear prediction systems reducing tool failures by 25%
- 15% annual increase in smart tooling adoption rates
Best Practices for Implementation
Success in aerospace machining requires a systematic approach:
- Regular monitoring of cutting parameters and tool wear patterns
- Implementation of appropriate cooling strategies for temperature management
- Consistent quality control measurements throughout the machining process
- Proper tool handling and storage protocols to maintain insert integrity
Conclusion
In aerospace manufacturing, where component integrity directly impacts flight safety, optimal tool selection transcends operational considerations. The continued evolution of advanced materials and smart technologies promises significant improvements in precision, reliability, and productivity across the aerospace sector.
Each insert type—carbide, ceramic, and PCBN—has its optimal applications, but successful implementation requires careful consideration of material properties, machining parameters, and economic factors. By understanding and appropriately applying the unique capabilities of each insert type, manufacturers can achieve an optimal balance of productivity, quality, and cost in their aerospace machining operations.
FAQ
Carbide is versatile and cost-effective, ceramic excels in high-speed hard material cutting, and PCBN offers superior performance in hardened steel applications but at a higher cost.
It depends on the application. Carbide is cost-effective for general use, ceramic increases productivity in hard metal cutting, and PCBN, though expensive, provides long-term value in precision work.
High-quality inserts boost machining efficiency, reduce downtime, and extend tool life, leading to increased productivity and lower operational costs.
Ceramic inserts generate less waste due to longer service life, while carbide and PCBN have a higher environmental impact due to manufacturing and disposal factors.
Carbide has moderate tool life and lower costs, ceramic lasts longer in abrasive conditions, and PCBN offers the best longevity for precision machining but with higher initial and maintenance costs.
Ceramic and PCBN excel in high-speed, high-temperature conditions, while carbide is better suited for moderate speeds with lower thermal resistance.
Follow Us:
Latest Posts
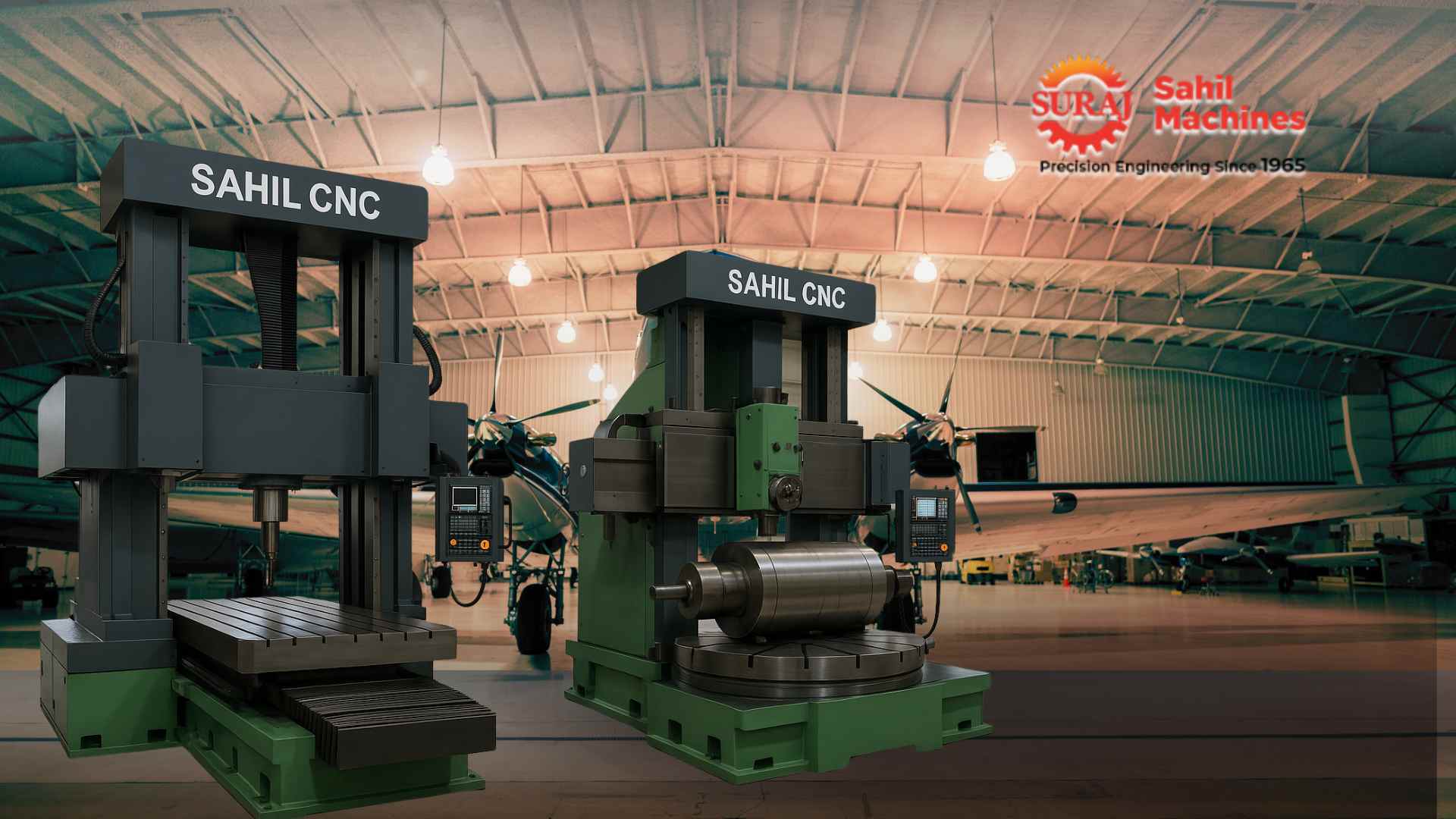
Revolutionizing Heavy Engineering: How Sahil CNC’s Double Column Milling and VTL Machines Transformed Large-Scale Manufacturing
by Admin - April 9, 2025
Get in touch with us about anything.
Connect with our team to explore the alloy solutions and machinery expertise you need.